Copps Industries offers a full range of standard and custom epoxy resin systems that can be used in composite manufacturing processes including, but not limited to infusion, hand-laminating, filament winding, RTM, and pultrusion.
Composite Material – Lightweight and high strength, composites are a result of a combination of two or more materials that still retain their macro-structure. This combination results in materials that have a stronger combined physical property than that of their individual ones.
Epoxy Resin
Epoxies are thermoset resins used in the manufacture of composite parts and structures, offering very good adhesion properties, high adaptability, low shrinkage, high strength, resistance to corrosive liquids and environments, good electrical properties, reliable performance at high temperatures, and adhesion to various substrates.
Composite Manufacturing from Copps Industries
- HP-RTM – RTM – High Pressure Resin Transfer Molding — One of the most modern methods for the mass production of composite parts, this is typically used to mold components with large volume, various shapes, sizes and smooth finish on both sides of the part. The HPRTM process can be automated which involves five steps: creating the preform, preform layup, closing mold, injection phase, and curing phase. HPRTM is rapidly becoming popular in the automotive, industrial, and agriculture industries.
- VARTM – Vacuum Assisted Resin Transfer Molding Process —This is a closed-mold manufacturing process (a variation of resin transfer molding) in which the top portion of a mold tool is replaced with a flexible vacuum bag, and vacuum only, no injection, is used to assist in resin flow. A vacuum facilitates resin flow into a fiber layup contained within a mold tool covered by a vacuum bag. Material thickness under full vacuum dictates the part thickness. After impregnation, the composite part cures at room temperature.
- LRTM – Light RTM – Light Resin Transfer Molding —This involves a closed-mold process similar to resin transfer molding. A vacuum holds the A and B molds together and produces two finished sides of the part with consistent and fixed part thickness. Dry fiber reinforcements are loaded into the A mold, the A mold is placed onto the B mold, and a vacuum ring around the tool holds them together. All of the air is vacuumed out of the part with a lower vacuum level, separate from the tool hold-down, and the resin is injected into the part. The tool stays under vacuum until the resin is cured.
- Vacuum Infusion Process (VIP) — Another closed-mold process, resin infusion occurs when a vacuum draws resin into a dry fiber laminate in a one-sided mold. A rigid or flexible film membrane is placed over the top and sealed around the periphery of the mold. Popular infusion resin types include epoxy, polyester, and vinyl ester.
- Pultrusion Process — A continuous process for composite materials manufacturing, pultrusion is achieved by pulling the material through a die/mold. The Pultrusion process involves a nonstop roll of reinforced fibers/mat, resin impregnator, die and heat source, and a continuous cutting/pulling system. This process is best suited for high volume single direction reinforced products like rods, poles, trim, flat panels, etc…
- Filament Winding —Filament winding is the process of winding resin-impregnated strands of fiber around a rotating mandrel to create a composite structure. Because different fibers and resins are used — and various winding techniques are employed — this process creates high-fiber loading with good directional strength. The resulting composite products are extremely strong.
- Hand Layup Process —Hand layup is a molding process in which fiber reinforcements are wet out by hand and then positioned manually into the mold. It’s the simplest composite molding method, and allows for simple processing, a wide range of part sizes, low-cost tooling, and easy part layup changes.
- Vacuum Bagging (Wet Bagging) — Vacuum bagging (including wet bagging) is a second step variation used in open molding and is a technique that creates mechanical pressure on a laminate during its cure cycle. A vacuum bag is placed over the hand laid part, similar to that of VIP, and then full vacuum is placed on the cavity as it cures. This allows for a more simple process like hand layup without the technical difficulties of VIP while still achieving higher than normal properties of a hand laid
Learn More
Copps Industries can custom formulate a variety of different epoxy resins to meet your specific needs; carbon fiber resin systems, fire-resistant (FR) resin, toughened resin, fiberglass resin systems, adhesives, and other. Performance fiber resin solutions are all in our realm of capabilities.
To learn more about our offerings and discuss how the techniques outlined above can help with your unique application needs, reach out to the team today.
Laminating Systems |
---|
Product | Components | Mix Ratio, pbv | Mixed Viscosity, cP @25C (77F) | Gel time @22C (72F), minutes | Set Time, hours | Tg,DSC, F ( C) | Safety Data Sheet(SDS) | Technical Specs |
---|---|---|---|---|---|---|---|---|
Low Viscosity, Fast (A-011/B-208) |
2 part, clear | 4/1 | 1,210 | 20 | 4 | 140 (60) | Login to access the Safety Data Sheets (SDS) |
|
Low Viscosity, Medium (A-011/B-209) |
2 part, clear | 3/1 | 960 | 30 | 8 | 129 (54) | Login to access the Safety Data Sheets (SDS) |
|
Low Viscosity, Slow (A-011/B-210) |
2 part, clear | 2/1 | 580 | 105 | 14 | 117 (47) | Login to access the Safety Data Sheets (SDS) |
|
High Viscosity, Fast (A-018/B-208) |
2 part, clear | 4/1 | 8,600 | 14 | 3-4 | 218 (103) | Login to access the Safety Data Sheets (SDS) |
|
High Viscosity, Medium (A-018/B-209) |
2 part, clear | 3/1 | 6,300 | 23 | 6-7 | 200 (93) | Login to access the Safety Data Sheets (SDS) |
|
High Viscosity, Slow (A-018/B-210) |
2 part, clear | 2/1 | 2,500 | 45 | 10-12 | 173 (78) | Login to access the Safety Data Sheets (SDS) |
RTM – Infusion – Injection Systems |
---|
Product | Components | Mix Ratio, pbv | Mixed Viscosity, cP @25C (77F) | Working time @22C (72F), minutes | Tensile Strength, psi | Tg,DSC, F ( C) | Safety Data Sheet(SDS) | Technical Specs |
---|---|---|---|---|---|---|---|---|
Fast Infusion (A-298/B-224) |
2 part, clear | 3/1 | 288 | 25 | 11,000 | 202 (94.6) | Login to access the Safety Data Sheets (SDS) |
|
Medium Infusion (A-298/B-225) |
2 part, clear | 3/1 | 291 | 120 | 10,300 | 207 (97.4) | Login to access the Safety Data Sheets (SDS) |
|
Slow Infusion (A-298/B-226) |
2 part, clear | 3/1 | 290 | 210 | 10,200 | 202 (94.3) | Login to access the Safety Data Sheets (SDS) |
|
LRTM Rapid Cure system, (A-013/B-223) | 2 part, clear | 4/1 | 330 | 10 | 9,600 | 165 (74) | Login to access the Safety Data Sheets (SDS) |
|
LRTM Fire Resistant Rapid Cure System, (A-033/B-223) | 2 part, clear | 4/1 | 430 | 10 | 8,600 | 159 (70.4) | Login to access the Safety Data Sheets (SDS) |
|
High Tg Infusion system, (A-233/B-451) | 2 part, clear | 4/1 | 620 | 90 | 8,600 | 301 (149.7) | Login to access the Safety Data Sheets (SDS) |
Structural Strengthening Systems |
---|
Product | Components | Mix Ratio, pbv | Mixed Viscosity, cP @25C (77F) | Working time @22C (72F), minutes | Tensile Strength, psi | Tg,DSC, F ( C) | Safety Data Sheet(SDS) | Technical Specs |
---|---|---|---|---|---|---|---|---|
Fast -SS (A-018/B-425) |
2 part, clear | 2/1 | 900 | 60-90 | 10,800 | 172 (78) | Login to access the Safety Data Sheets (SDS) |
|
Slow-SS (A-018/B-435) |
2 part, clear | 2.6/1 | 620 | 180-240 | 10,200 | 193.5 (90) | Login to access the Safety Data Sheets (SDS) |
Filament Winding Systems |
---|
Product | Components | Mix Ratio, pbv | Mixed Viscosity, cP @25C (77F) | Working time @22C (72F), minutes | Tensile Strength, psi | Tg,DSC, F ( C) | Safety Data Sheet(SDS) | Technical Specs |
---|---|---|---|---|---|---|---|---|
High Tg Filament winding system, (A-10012/B-10012) | 2 part, clear | 1.18/1 | 1,400 | 24 hours | 8,400 | 341 (171.5) | Login to access the Safety Data Sheets (SDS) |
|
High Tg Pultrusion System, (A-30400/B-29000) | 2 part, clear | 1/1 | 5,700 | 24 hours | 5,700 | 272 (133.2) | Login to access the Safety Data Sheets (SDS) |
Pultrusion Systems |
---|
Product | Components | Mix Ratio, pbv | Mixed Viscosity, cP @25C (77F) | Working time @22C (72F), minutes | Tensile Strength, psi | Tg,DSC, F ( C) | Safety Data Sheet(SDS) | Technical Specs |
---|---|---|---|---|---|---|---|---|
High Tg Pultrusion System, (A-30400/B-29000) | 2 part, clear | 1/1 | 5,700 | 24 hours | 5,700 | 272 (133.2) | Login to access the Safety Data Sheets (SDS) |
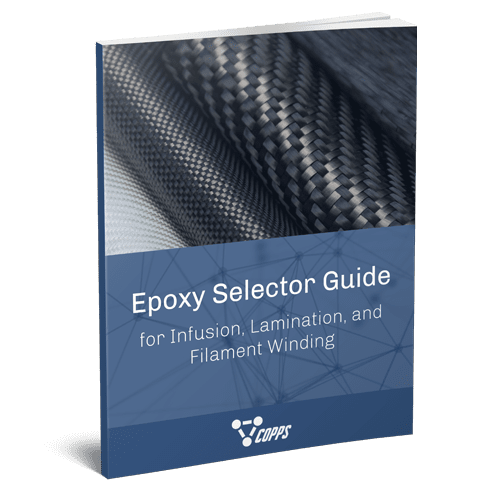
Download Our eBook
Selecting the appropriate epoxy for your composite application should be a streamlined and uncomplicated process. Our Epoxy Selector Guide for Infusion, Lamination, and Filament Winding will help you select an ideal resin that meets the necessary criteria of your application.
Learn More