At Copps Industries, we provide custom-formulated epoxy and polyurethane solutions to customers in the industrial and OEM markets.
Our extensive design and manufacturing experience and state-of-the-art manufacturing plant allow us to tailor each product solution to accommodate the unique needs of the application while delivering process improvement savings of 15–50%. By providing custom solutions, we help streamline processes, lower shipping, warehousing, and storage costs, and improve user safety.
An Epoxy is formed by mixing an epoxy resin and a hardener, similarly a Urethane is formed by combining a polyol resin with a curing agent. Our products are available in a wide range of formulations, all of which feature characteristics that make them suitable for different applications. As such, when choosing adhesives, potting compounds, and other systems, it is important to vet your options with regard to the requirements and restrictions of your application. Some of the questions you need to ask yourself include:
- Which uncured property (e.g., viscosity, color, worklife, and cure time) and cured (adhesive properties, durability, and flexibility) properties are most important for your application?
- What process or system will the epoxy or urethane compound be used in?
- Does my system need to adhere to any testing standards (e.g., ASTM, UL)?
- What are the pre-curing, curing, and post-curing requirements for my application?
- Do I have an existing epoxy/urethane system in place? If so, how does it impact or limit my processes and manufacturing goals?
- What are my key application specs for my system?
At Copps Industries, we offer more than 2,500 custom-designed epoxy and urethane adhesives, coatings, potting, and encapsulation compounds formulated to accommodate diverse industrial and original equipment manufacturer (OEM) needs. Our one- and two-component, heat cure, ambient cure, and high-temperature epoxy and urethane systems are available in a wide range of viscosities from very low to a non-sag paste.
The following guide will help you determine which epoxy or urethane solution is appropriate for your industrial or OEM application.
Solutions for Industrial and OEM Applications
Epoxy and Urethane systems—including adhesives, coatings, potting, and encapsulation compounds—find use in a variety of industrial and OEM applications, including, but not limited to, the following:
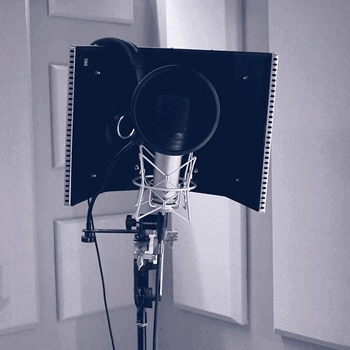
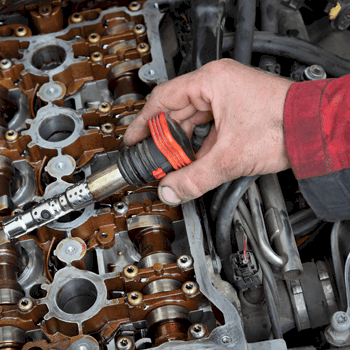
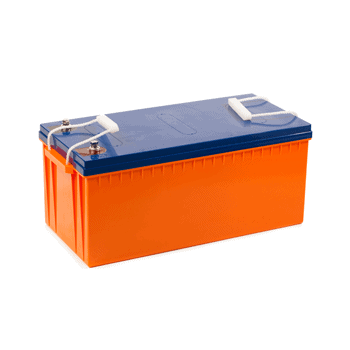
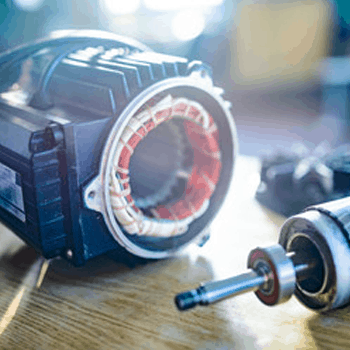

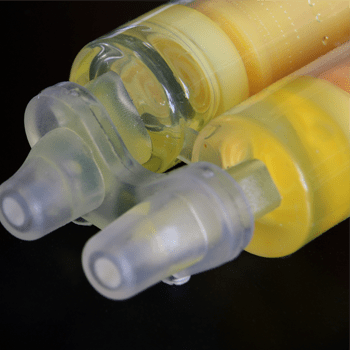
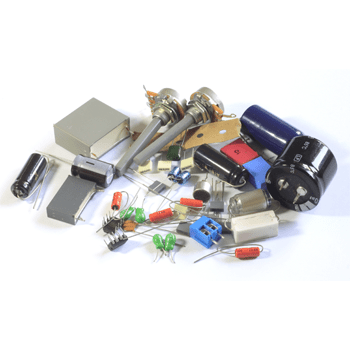
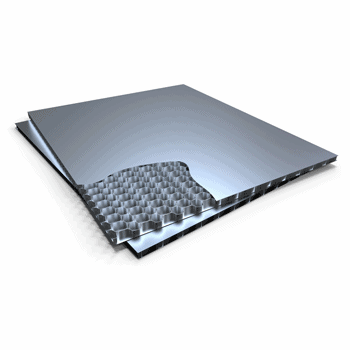
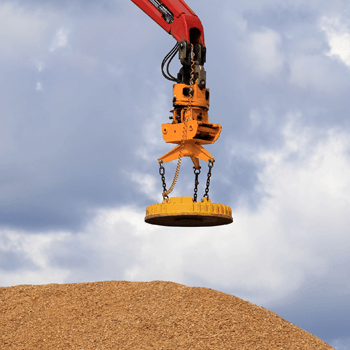
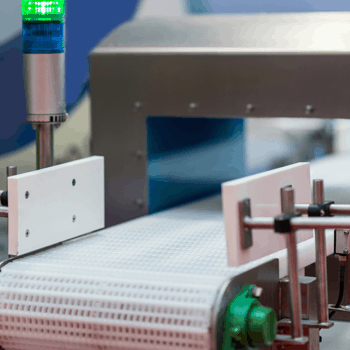
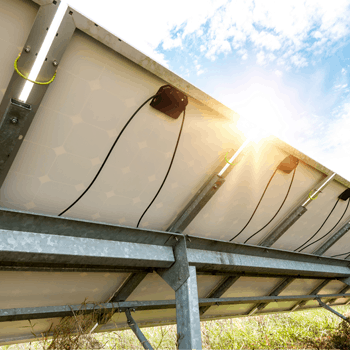
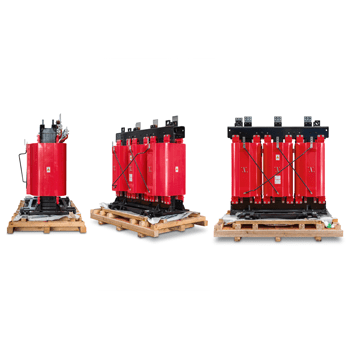
Handling Properties
Handling properties refer to its pre-cured properties—i.e., what it is like before it is cured. Some of the key handling characteristics to consider when choosing an epoxy or urethane are:
Viscosity
Viscosity is the tendency of a fluid to resist flow. This characteristic affects the material’s thickness and consistency, which, in turn, influences how well it permeates a substrate. The units used for viscosity measurements are Centipoise (cps) or millipascal-second (mPa-s).
Epoxies and Urethanes are Non-Newtonian fluids, meaning their viscosity changes depending on the shear rate. Their viscosities are normally measured using a Brookfield viscometer, which calculates viscosity by considering the relationship between shear rate, time, and temperature. Epoxies and Urethanes can be classified into three categories based on their viscosity:
- Low-viscosity: Low-viscosity systems have viscosities less than 2,000 cps. They have the thickness and consistency of water to detergent, meaning they have excellent flow, penetration, fill, and air release properties. Typical industrial and OEM applications include coatings, ignition coils, and insulation varnish.
- Medium-viscosity: Medium-viscosity systems have viscosities between 2,000–50,000 cps. They have the thickness and consistency of honey to ink, meaning they offer less flow and penetration and better mechanical strength and thermal conductivity than their low-viscosity counterparts. Typical industrial and OEM applications include electrical potting and encapsulation, filter end caps, switches and connectors, and transformers.
- High-viscosity: High-viscosity systems have viscosities greater than 50,000 cps. They have the thickness and consistency of ketchup to shortening, meaning they exhibit non-sagging and non-drip characteristics. Other key properties include excellent resilience, adhesion, heat and shock resistance, and thermal conductivity. Typical industrial and OEM applications include adhesives for chillers and filter end caps.
Mix Ratio
As indicated above, these systems are a mixture of a resin and a hardener. The proportion of resin to hardener required to cure or hardened and in turn perform properly is referred to as the mix ratio. This relationship depends on the exact chemical formula of the two compounds. It can be indicated in several ways:
- Weight ratios (e.g., 10 grams of resin and 10 grams of hardener)
- Volume ratios (e.g., 1 cup of resin and 1 cup of hardener)
- Non-fractional ratios (e.g., 2 parts resin to 1 part hardener)
- Fractional ratios (e.g., 2.3 part resin to 1 part hardener)
Color
The color of a system can be tailored to the needs of an application by adding different fillers and pigments. Unfilled resin systems have no fillers added, so they maintain the natural color of the resin. Filled resin systems have fillers added, so they take on the color(s) of the filler(s). Some systems are naturally clear. They can be used as-is or mixed with pigments to achieve a specific color.
Cure Requirements
Curing is the chemical process by which an epoxy or urethane hardens and develops its full strength. The time it takes to cure fully—i.e., the cure time—depends on several factors, such as formulation and temperature. Some systems cure at room temperature once the resin and hardener are mixed, while others require elevated temperatures (generally between 200° to 350° F) to achieve a full cure.
The curing process occurs in stages. The initiation stage is the period of time in which the resin and hardener are mixed, but the mixture remains flowable and workable. The mixture must be applied before this stage ends. The gel time, or initial cure stage is the first point in time at which the mixture begins to transition into a solid. The final stage, or full cure stage is when the product has had enough time and or temperature applied for the chemical reaction to reach its full potential.
Cured Physical Properties
Ultimately, the type of system you choose should demonstrate the physical properties required for your application. Some of the characteristics you may consider include:
- Adhesion
- Durability
- Thermal conductivity
- Flame retardance
- Flexibility
- Mechanical strength
- Electrical conductivity
How these properties are prioritized affect which resin and hardener formulation best suits your application. A knowledgeable and experienced solutions partner can formulate a system to suit your project needs.
Contact Copps Industries for Industrial and OEM Epoxy Solutions Today
Epoxy and Urethane systems play a critical role in countless industrial and OEM applications. If you’re looking for a reliable solutions provider, turn to the experts at Copps Industries. For additional information about our custom epoxy and urethane solutions for industrial and OEM applications, contact us today. To discuss your application with one of our representatives or receive a tailored recommendation or custom formulated product, request a quote.
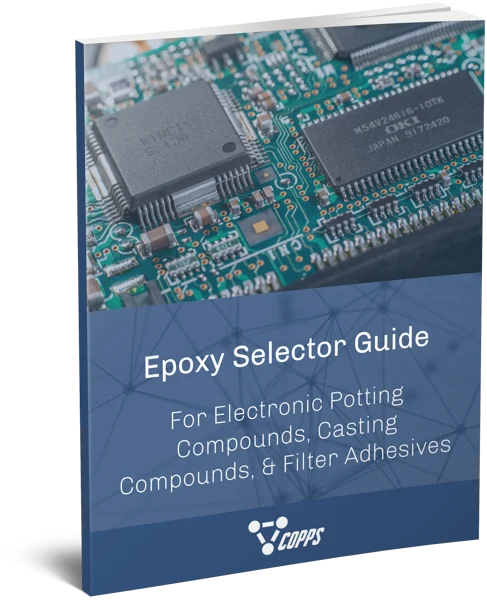
Download Our eBook
Epoxy and polyurethane systems can be custom formulated to your application requirements. Our Epoxy Selector Guide for Industrial/OEM Applications will help you to select an ideal urethane or polyurethane system to meet the necessary criteria.
Learn More