Category Archive: Services & Capabilities
Composite materials have seen remarkable advancements across a range of industries in recent years. From automotive and aerospace to construction and defense, the demand for innovative, high-performing composite solutions is steadily growing.
At Copps Industries, our experts and chemists work continuously to stay ahead of trends and meet the evolving needs of our customers. We’re helping to lead the conversation on where composites stand today and where they’re headed tomorrow.
Here are the Top 4 Trends we see shaping the future of composites:
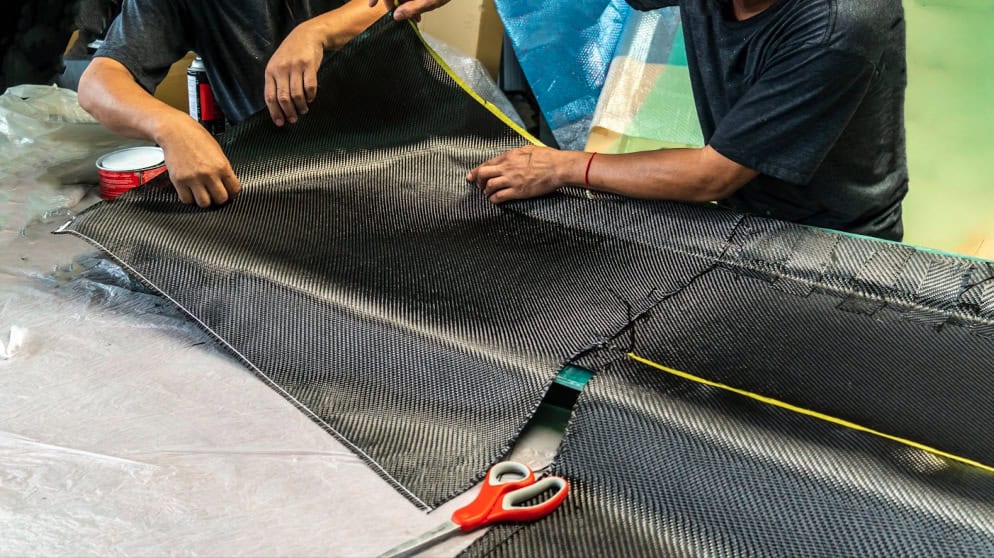
Trend #1: Sustainability and Recyclability
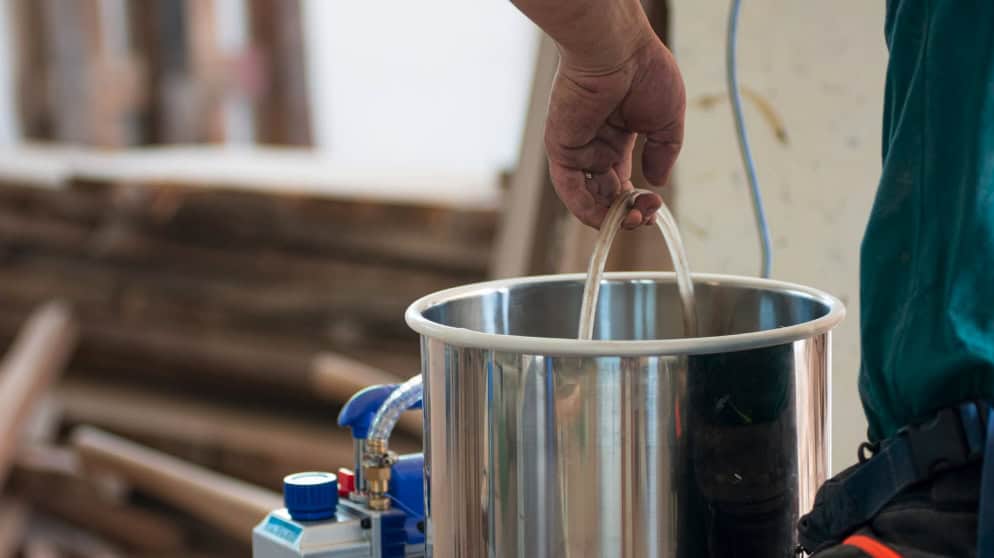
As sustainability becomes a global priority, the demand for bio-based and recyclable composite materials is rising. This trend is especially significant in the automotive and construction industries, where there is a pressing need for lightweight, high-performance materials that are also environmentally responsible.
One of the key challenges is addressing the end-of-life phase for composite materials, particularly in automotive, where vehicles have a typical lifespan of 12 years. The industry always seeks solutions to recycle composite materials, minimize waste, and reduce environmental impact.
At Copps Industries, we’re committed to supporting this push forward. Our team continually explores sustainable solutions to ensure our products not only meet performance standards but also help reduce environmental impact across industries.
Trend #2: Advanced Manufacturing Techniques
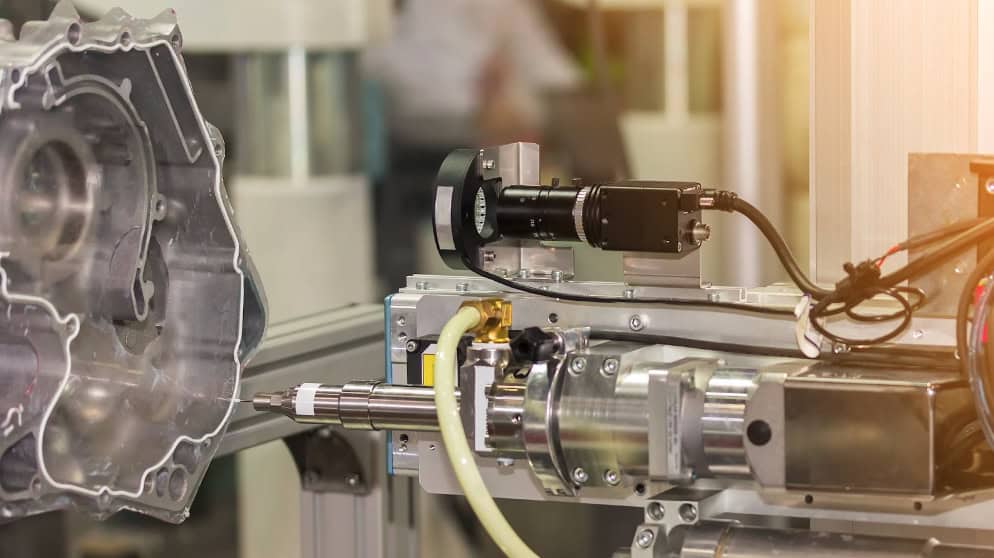
Automation and advanced manufacturing techniques are revolutionizing production in nearly every industry. Automation is a game-changer that can reduce cycle times and manufacturing costs—factors that are sometimes even more significant than the cost of materials themselves.
While automation remains the largest focus, we’re also seeing AI and machine learning emerge as innovative tools. These technologies have the potential to deliver increased precision and enable smarter, more efficient production processes.
At Copps Industries, we don’t just provide top-tier formulations—we also work with our customers to optimize their processes. Through close collaboration, we can help you imagine strategies that reduce waste, enhance production speed, and ultimately improve the bottom line.
Trend #3: High-Performance Composites for Extreme Conditions
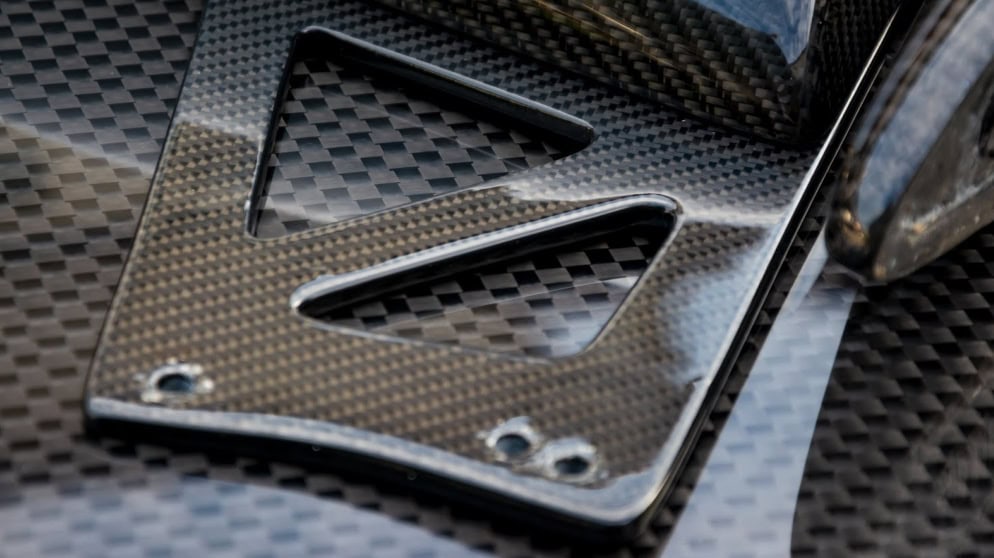
Composites designed for extreme conditions have become increasingly critical in industries such as aerospace, defense, and marine. These sectors require materials that offer improved strength and durability in the most demanding environments. Innovations in high-performance composites are enabling industries to develop lighter, stronger materials that boost performance and contribute to sustainability by reducing fuel consumption and emissions.
Copps Industries strives for excellence in developing high-performance composites. Our products help customers push the boundaries of what’s possible, from aerospace components that can withstand extreme temperatures to marine materials designed for deep-sea endeavors.
Trend #4: Design Standards and Specifications
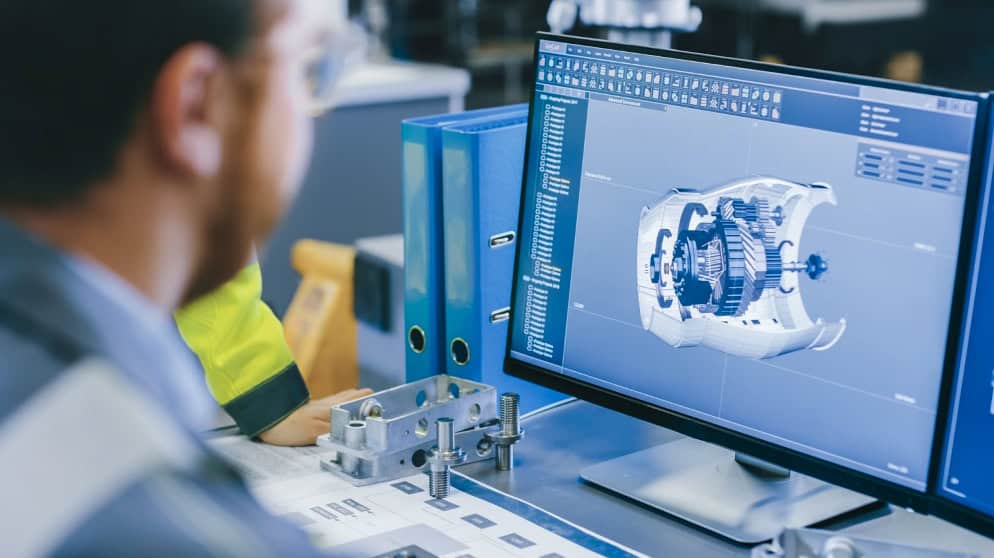
Unlike metals, composites lack globally fixed design standards and specifications, making the process of testing and verification more complex. This adds time and cost to projects, as every new material or design requires rigorous testing to ensure it meets safety and performance standards. The absence of uniform standards poses both a challenge and an opportunity, as companies have to find tailored solutions to meet their specific project needs.
At Copps Industries, we navigate this challenge by working closely with our customers to ensure their composite solutions are thoroughly tested and verified for every application. Our experience in customization and relentless commitment to quality allow us to help you overcome this barrier.
Copps Industries: Your Partner in Innovations
At Copps Industries, we’re not just addressing today’s challenges—we’re anticipating tomorrow’s trends. Our commitment to innovation ensures we’re always at the forefront of industry developments, providing customized solutions for every unique need. Whether your focus is on sustainability, advanced manufacturing, high-performance composites, or stringent design standards, we’re committed to your success.
Contact us today to learn more about our solutions and how we can help you stay ahead of the curve in composites.
Marine environments are some of the most demanding on the planet, presenting unique challenges like constant exposure to harsh conditions and rapid corrosion from saltwater. For our customers in the marine industry, their most common concerns include increasing durability, reducing weight, and continuously finding ways to reduce costs.
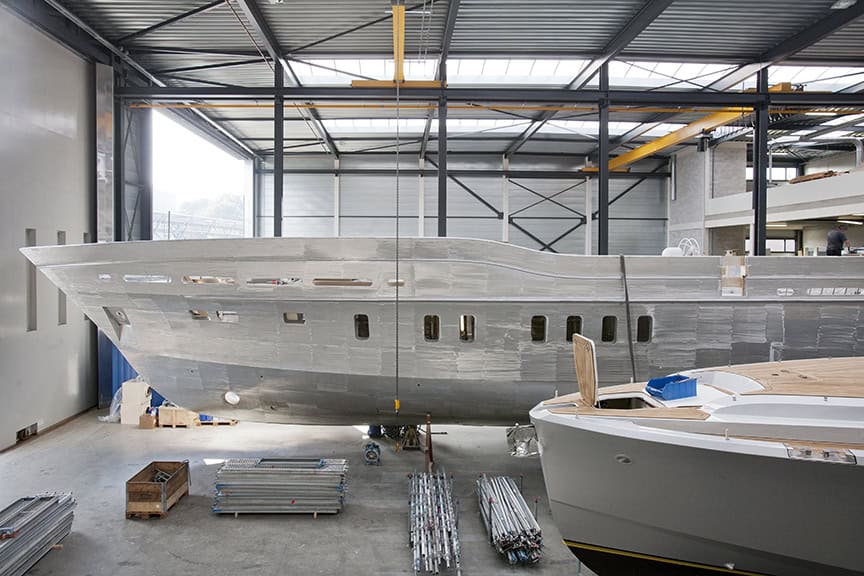
At Copps Industries, we understand these challenges. Our composite epoxy systems are tailored to meet the specific demands of marine environments, providing solutions that improve performance and extend the lifespan of marine structures. From waterproof and durable coatings to marine epoxy grouts, our products offer unmatched benefits in marine applications.
Let’s take a deeper dive into the key properties of marine epoxy solutions from Copps.
Corrosion Resistance and Durability
Saltwater, humidity, and temperature extremes are constant threats to marine structures. Traditional materials like steel and aluminum often suffer from corrosion, increasing the need for maintenance and repairs. Composite epoxies, however, are designed to resist corrosion, providing a long-lasting barrier that significantly reduces the cost of upkeep.
In the marine context, durability refers to impact resistance and long-term structural integrity. Imagine a boat hull repeatedly hitting the water—Copps’ composite epoxies ensure the structure remains intact over time, offering superior protection against the stresses of the sea.
Our epoxies are ideal for:
- Boat and Ship Construction: Copps’ epoxy resins offer superior bonding, laminating, and reinforcement for various materials in boat and ship construction. Their water and chemical resistance make them ideal for key structural components.
- Coating Applications: Our marine-grade epoxy resins create protective coatings for a durable, corrosion-resistant layer. These coatings can be used on ballast tanks, hulls, decks, and cargo tanks, ensuring marine vessels maintain their structural integrity.
Lightweight and High Strength
Weight reduction is critical for improving fuel efficiency and performance in marine applications. The lighter a vessel, the more payload it can carry and the less fuel it consumes. Composite epoxy systems offer an exceptional strength-to-weight ratio, allowing for significant weight reduction without compromising structural strength.
However, there’s a balance to strike between weight reduction and durability. While certain marine components could be made many times lighter, it’s important also to maintain the necessary strength to withstand the harsh marine environment. Copps’ epoxy systems truly shine at this intersection of strength and durability.
Our epoxies are ideal for:
- Fuel Efficiency and Performance: Reducing the weight of boat hulls, marine decks, and subsea structures enhances performance and leads to lower fuel consumption, benefiting both the environment and operating costs.
- Load-Bearing Applications: The strength-to-weight ratio of our composite epoxies makes them ideal for load-bearing applications in marine environments, offering significant performance improvements without sacrificing durability.
Adhesion and Flexibility in Applications
One of the standout features of composite epoxy systems is their excellent adhesion. This allows for bonding dissimilar materials—such as metals and plastics—frequently used together in marine construction. Additionally, epoxy systems absorb vibrations, preventing fatigue in structures subjected to constant movement, such as ships and underwater pipelines.
It’s important to note that flexibility in the context of marine epoxies refers to the epoxy systems’ design capabilities, not the material’s physical flexibility. Application flexibility allows for the creation of complex structures that can withstand the rigors of the marine environment.
Our epoxies are ideal for:
- Maintenance and Repair: Copps’ composite epoxy products are effective for repairing cracks, filling voids, and underwater repairs. They provide strong adhesion and durability to address common marine issues like hull damage, water intrusion, and structural reinforcement, which maintains the longevity of marine vessels.
- Watertight Seals and Repairs: Whether repairing hulls or creating watertight seals for subsea pipelines, our epoxy systems offer unmatched flexibility in addressing a range of marine-related needs.
Solutions for Marine Applications from Copps Industries
At Copps Industries, we’re dedicated to providing the marine industry with products that focus on durability, weight reduction, and versatility. Our marine-grade epoxy resins are specifically formulated to withstand the challenges of marine environments, and we continue to innovate to meet the evolving needs of our customers.
Whether you’re building new vessels, reinforcing existing structures, or looking for solutions that reduce maintenance costs, Copps has the expertise and products to deliver high-performance marine solutions. For more information on how our products can benefit you, contact us or request a quote today.
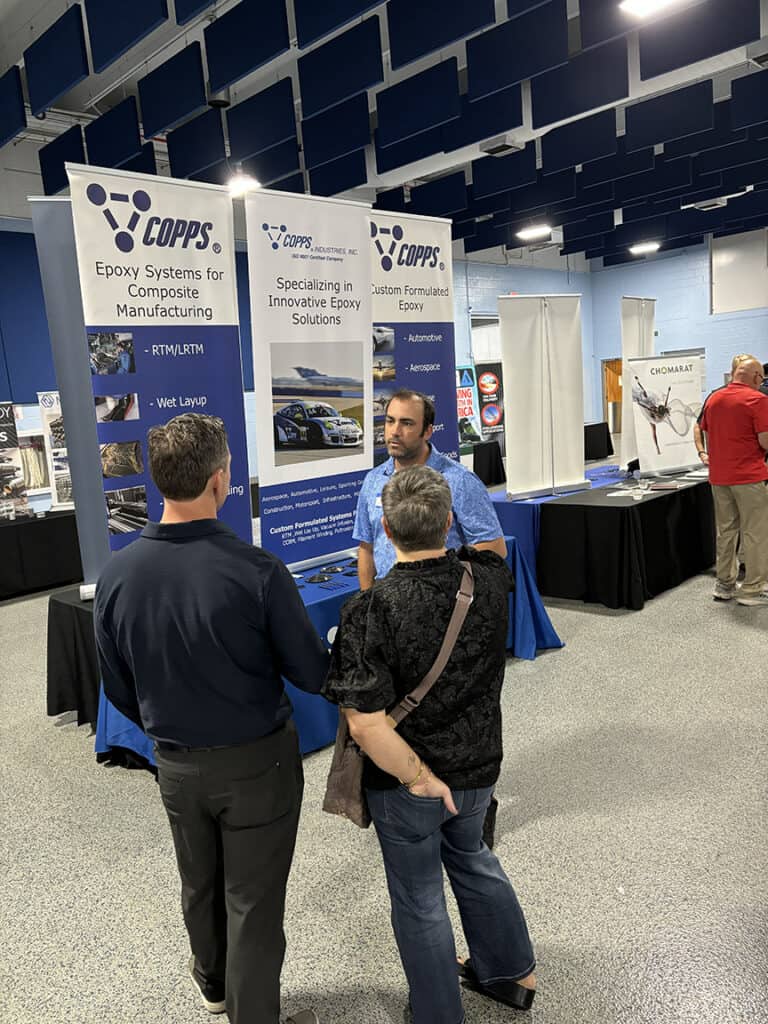
On October 9, professionals and innovators from across the composites industry gathered for the SAMPE Carolinas 2024 Material Expo in Charleston, South Carolina. The theme of ‘Next Generation Composites’ set the stage for insights on the latest trends and future breakthroughs in composite materials.
Our own Brian Gardner is a director of the SAMPE Carolinas Chapter, and Copps Industries is a chapter sponsor. Our support of SAMPE and leadership in the organization is one more example of Copps’ efforts to move the industry forward.
The one-day expo brought together leaders from across industries to showcase how composites are revolutionizing everything from aerospace to transportation. Here are our highlights and insights from the event:
Global Outlook for Composites in Aerospace
Eric Pierrejean, CEO of JEC, kicked off the presentations with an overview of the current state of composites in aerospace. He explored how new materials and technologies are driving performance improvements and sustainability. He emphasized some of the top trends we’ve seen in the industry, such as an increased demand for lighter, stronger composites.
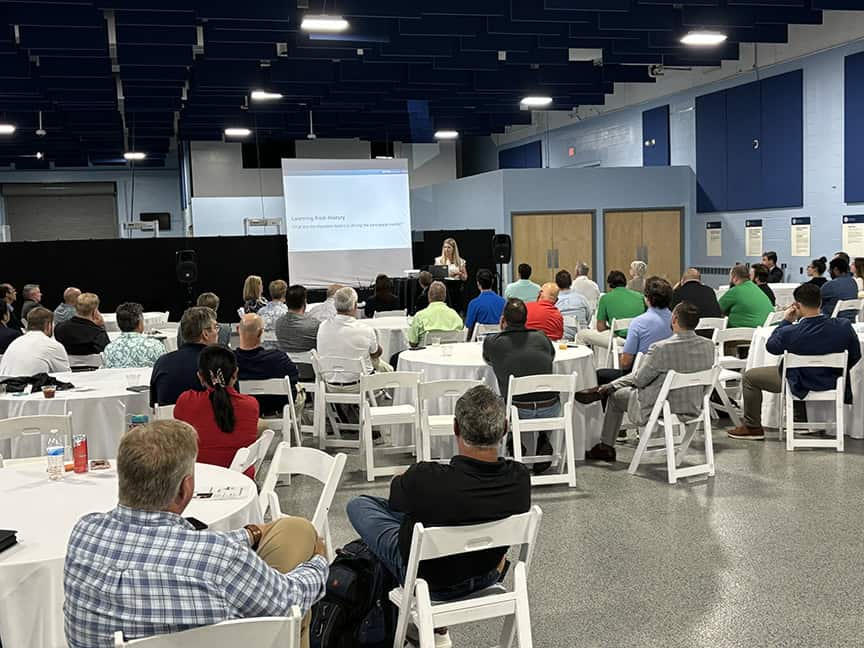
Development of Autonomous Rail Systems
A presentation from Dr. Tim Luchini, CEO of Intramotev, discussed how composites are being integrated into the development of autonomous rail systems. His talk revealed how lightweight composites are crucial to making autonomous, energy-efficient trains a reality. He showcased the potential of composites to improve performance and reduce the carbon footprint of the rail industry.
Emerging Voices in Composites
Participants at the expo also heard from emerging talent in the field. Ashley Tracey, a project engineer at Boeing, shared her insights on how Boeing is leveraging composites in its new aircraft models to address unique engineering challenges. Trent Miller, a student at the University of South Carolina and the 2024 Scholarship Winner, gave us a glimpse of the future of composites through the lens of an undergraduate researcher.

Key themes throughout the expo focused on:
- The growing importance of sustainability in manufacturing.
- How technology is driving innovations in composite production.
- The importance of partnership to accelerate innovation and address future challenges.
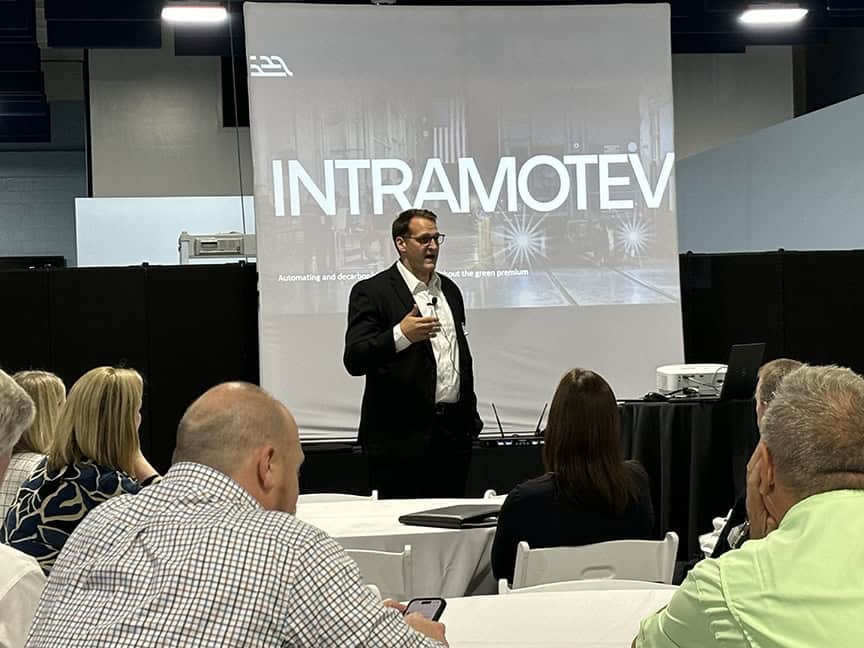
Looking Ahead to the Future of Composites
As the SAMPE Carolinas 2024 Material Expo drew to a close, it was clear that composites will continue to play a crucial role in the future of industries like aerospace, rail, and beyond. The event highlighted the need for continuous innovation and collaboration as we look toward the next generation of composite materials.
At Copps Industries, we’re committed to staying ahead of the curve by developing solutions that meet the evolving needs of industries that rely on composite materials. As we look forward, our team of experts is excited to push the boundaries of what composites can achieve.
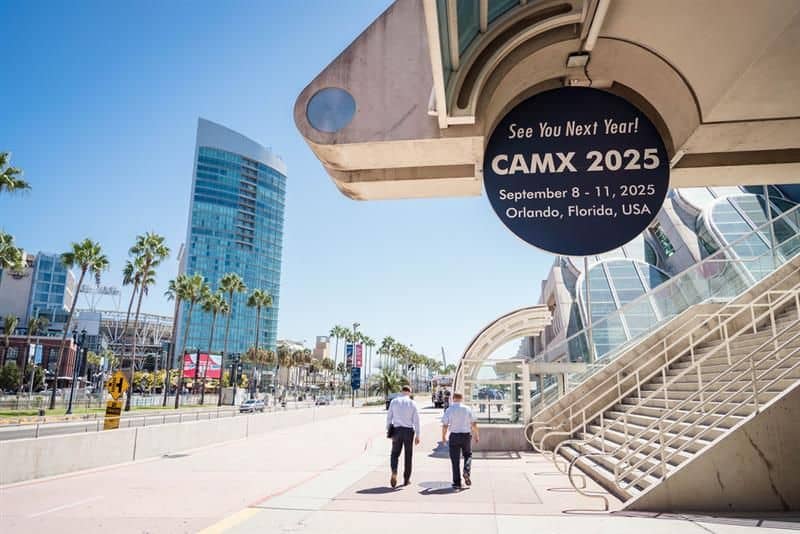
CAMX—the Composites and Advanced Materials Expo—is the largest and most comprehensive composites and advanced materials event in North America. Created by the American Composites Manufacturers Association (ACMA) and the Society for the Advancement of Material and Process Engineering (SAMPE), CAMX is where professionals come together to share innovations, connect business ideas, and drive the future of their industries.
Copps Industries was excited to attend CAMX 2024, held in San Diego, California, from September 9-12. The event brought together the experts, ideas, and science that are creating the materials and products of the future. With a variety of speakers, education, and an expansive expo, the conference offered access to solutions, networking, and advanced industry thinking.
Here, we’re sharing some of the highlights and key takeaways from this year’s event.
Celebrating 10 Years of Innovation
This year marked the 10th anniversary of CAMX, celebrating a decade of innovation, collaboration, and growth. The event has cemented its position as a must-attend gathering for those in composites and advanced materials. Over 500 exhibitors from across the globe showcased the latest products, technologies, and services, setting the stage for attendees to experience the future of innovation firsthand.
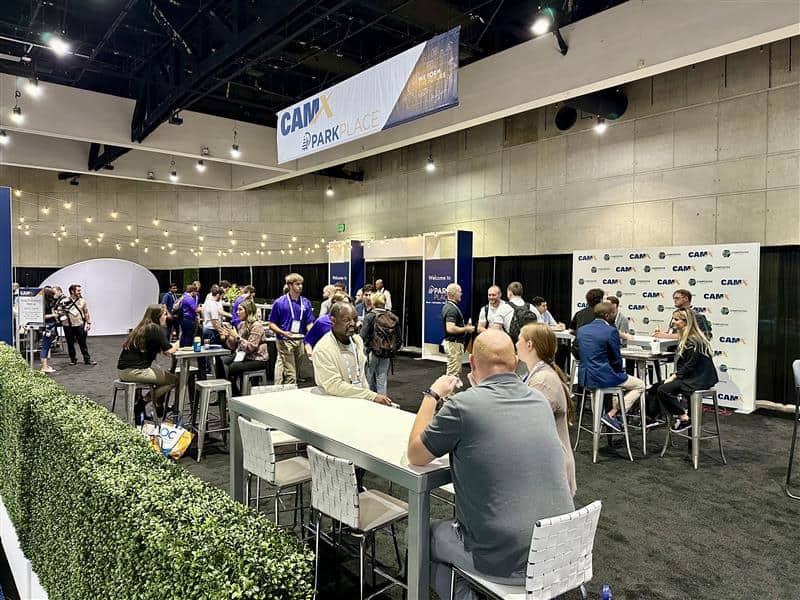
We Form the Future
CAMX showcased the cutting-edge technologies that are bringing concepts to life—such as 3D printing, advanced cutting machines, and live manufacturing processes. Designated space in CAMX Park Place allowed attendees to engage with peers, partners, and customers. It was an interactive experience designed to spark ideas, discuss common challenges, and collaborate on solutions across various fields.
Thought-Provoking Sessions and Presentations
The CAMX conference program featured insightful educational sessions and technical presentations. With topics ranging from fractural analysis to fused-granular fabrication using sustainable carbon fiber, the sessions highlighted the advancements shaping the composites industry. Noteworthy presentations included innovations in polyurethane systems for lightweight battery enclosures and composites with structural health monitoring capabilities.
Additionally, several sessions explored advancements in materials, bonding, joining technologies, sustainability, manufacturing processes, and more. These focused on practical applications and the future of composites across industries like aerospace, automotive, and construction.
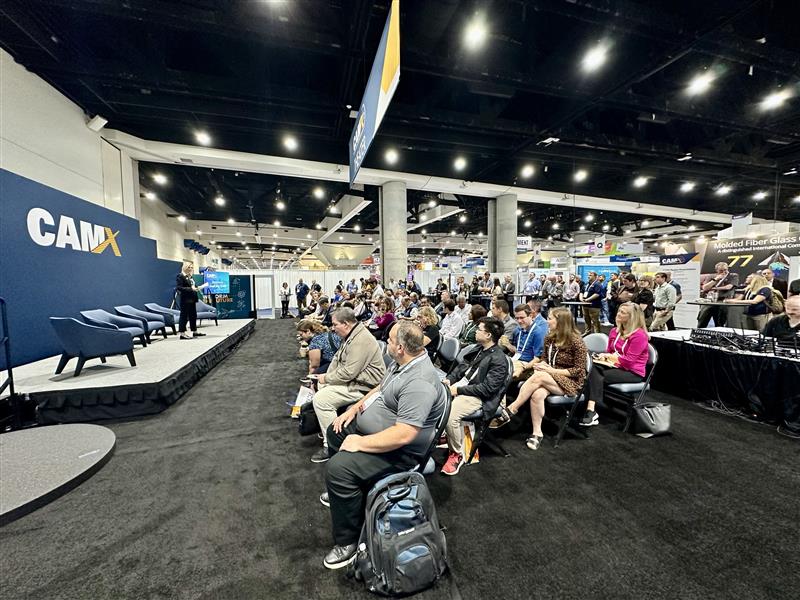
Keynote Address: Technologies Evolving the World Around Us
A standout moment at CAMX 2024 was the keynote address delivered by Maurice Conti, a globally recognized futurist and technology strategist. Conti discussed emerging technologies such as AI, augmented and virtual reality (AR/VR/XR), and advanced robotics, all with a focus on human-centered design and sustainability. His expertise, gained through collaborations with companies like Tesla, Amazon, and Airbus, offered insights into how technology can evolve to better serve humanity and industry.
Industry-Relevant Sessions
As always, CAMX sessions delved into pressing topics affecting the industry. A few standout sessions this year included:
- Low-cost manufacturing for military and commercial markets
- AI-driven innovations for materials development
- Design innovations enhancing safety and energy efficiency in transportation
- Automated composite inspection technologies
- Structural composites in modern construction
These sessions provided deep dives into the technologies and processes revolutionizing the composites and advanced materials industries.
Exhibit Hall: A Hub of Innovation and Engagement
The exhibition floor was a hub of activity, with manufacturers, suppliers, and innovators showcasing their latest advancements. For Copps Industries, the exhibit hall provided a valuable opportunity to meet face-to-face with potential customers, explore emerging market needs, and gain firsthand insights into the future of composites and advanced materials. We were able to foster connections with industry peers and discuss the future trends driving innovation forward.
Connecting to Copps Industries Values
At Copps Industries, we share the same focus on innovation and technological advancement as showcased at CAMX. We’re committed to keeping pace with the latest trends in composites manufacturing, product design, and materials engineering. The lessons learned and connections made at CAMX will inform our ongoing efforts to provide cutting-edge solutions that meet the evolving needs of our customers across multiple industries.
Looking Ahead
CAMX 2024 once again provided a valuable platform for collaboration, innovation, and knowledge sharing. From inspiring speakers to hands-on exhibits and technical sessions, the event showcased how the composites and advanced materials community is tackling today’s biggest challenges while seizing tomorrow’s opportunities. As a proud participant, Copps Industries is excited to continue driving innovation, ensuring we deliver value with forward-thinking solutions that shape the future.

In mining operations, every hour of unexpected downtime can translate into lost productivity and significant costs. Effective maintenance strategies not only keep your equipment running smoothly but also enhance your efficiency and overall operational effectiveness.
Here, we’re outlining best practices and state-of-the-art products for equipment maintenance in the mining industry, focusing on proactive approaches to maximize the reliability and performance of your equipment.
Best Practices for Equipment Maintenance
Proactive equipment maintenance strategies can help you minimize costly downtime and keep your operations running smoothly. Consider adopting these maintenance best practices to help you maintain productivity and minimize costs:
Implement Predictive Maintenance:
- Use condition monitoring tools such as wear sensors, vibration analysis, and oil analysis to predict equipment failures before they happen.
- Collect and analyze historical data to anticipate potential issues and schedule proactive maintenance.
Adopt Preventive Maintenance Programs:
- Establish a regular maintenance schedule based on manufacturer recommendations and your typical equipment usage.
- Perform routine inspections and servicing tasks to address wear and tear before it leads to equipment failure.
Develop a Comprehensive Maintenance Plan:
- Create detailed plans for maintaining each piece of equipment, outlining tasks, frequencies, and procedures.
- Include emergency response plans for unexpected breakdowns to minimize downtime.
Standardize Maintenance Procedures:
- Develop standard operating procedures (SOPs) for maintenance tasks to ensure consistency and efficiency.
- Use checklists and standardized documentation to streamline processes and reduce errors.
- Your SOPs should also outline the use of preferred products like Armor Plate wear-resistant coating and maintenance products.
Perform Root Cause Analysis:
- Investigate the root causes of equipment failures to address underlying issues and prevent them from recurring.
- Implement corrective actions based on your findings to improve your equipment reliability.
Optimize Parts and Product Inventory:
- Maintain an organized inventory of critical spare parts to reduce downtime associated with parts shortages.
- Use basic inventory management practices to forecast demand so the critical parts and products you need are always available.
Invest in Long-Term Performance:
- Focus on improving the reliability and durability of your equipment through ongoing upgrades, modifications, and quality improvements.
- Invest in high-quality components, technologies, and maintenance products that offer better performance and longevity.
- The right maintenance products—like Copps’ line-up of solutions—can prolong equipment lifespan by providing superior protection against erosion, corrosion, and wear.
Prioritize Safety and Operational Integrity:
- Promote a safety-first culture to ensure your maintenance practices align with regulatory standards and prioritize operational safety requirements.
- Invest in training to equip your team with knowledge of proper maintenance techniques and enhance their ability to troubleshoot problems.
Armor Plate Wear-Resistant Coating and Maintenance Products
Copps Industries provides a full range of wear-resistant and maintenance epoxy products to protect your equipment from deterioration over time. Our Armor Plate products feature abrasion- and corrosion-resistant epoxy compounds designed to repair, rebuild, and extend the life of equipment in industries ranging from mining to aggregate and more.
Our Armor Plate products can be used to repair and reinforce:
- Pump casings
- Cyclones
- Pipe elbows
- Slurry lines
- Vibrating screens
- Castings
- Shafts and propellers
- Chutes
- Screw conveyors
Copps Industries: Your Partner in Maintenance Excellence
At Copps Industries, our epoxy systems are engineered to help your equipment reach its full lifespan and deliver optimal performance. Used as a part of your proactive maintenance plans, our solutions can help you reduce equipment downtime, enhance productivity, and improve your overall operational efficiency.
Our line-up of ceramic and metal epoxy solutions protects a broad range of equipment from abrasion and wear, and we can provide custom solutions that effectively mitigate damage in nearly any application. For more information about our tailored solutions, contact us and request a quote.
In industrial maintenance and repair—especially in the demanding mining industry—there’s a critical need for reliable, high-performance materials. Whether you’re dealing with heavy machinery, critical structural components, or equipment exposed to extreme conditions, the right epoxy systems can make all the difference.
Copps Industries offers a full lineup of epoxy products designed to meet the toughest challenges, providing durability, rapid strength development, and exceptional protection against erosion, corrosion, and wear.
Here, we’re looking at four standout products from our lineup: REDBAC Deep Pour 3CE Grout, Maximum Performance Pumpable Grout, Armor Plate High-Performance Brushable Ceramic, and Armor Plate – Steel – Fast. From deep grouting large machine bases in mining operations to protecting pumps and impeller blades, these epoxy systems are engineered to deliver unmatched performance and longevity.
REDBAC Deep Pour 3CE Grout (K-028)
REDBAC Deep Pour 3CE Grout is a three-component, 100 percent solid epoxy resin system designed for pours up to 8″ (20.3 cm). Deep Pour 3CE offers rapid strength development, excellent flow characteristics, and minimal shrinkage. It flows into spaces under machines, fills completely before solidifying, and is self-leveling. It will survive impact and vibration equal to reinforced rubber materials and will not de-laminate under the most severe shock loads.
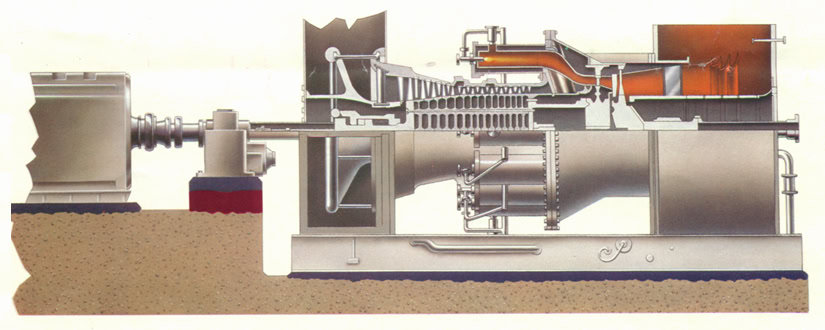
Common applications for Deep Pour 3CE include:
- Deep grouting of large machine bases
- Setting large pumps
- Setting large sole plates
- Deep repairs in foundations
- Use as a concrete alternative for critical machine settings
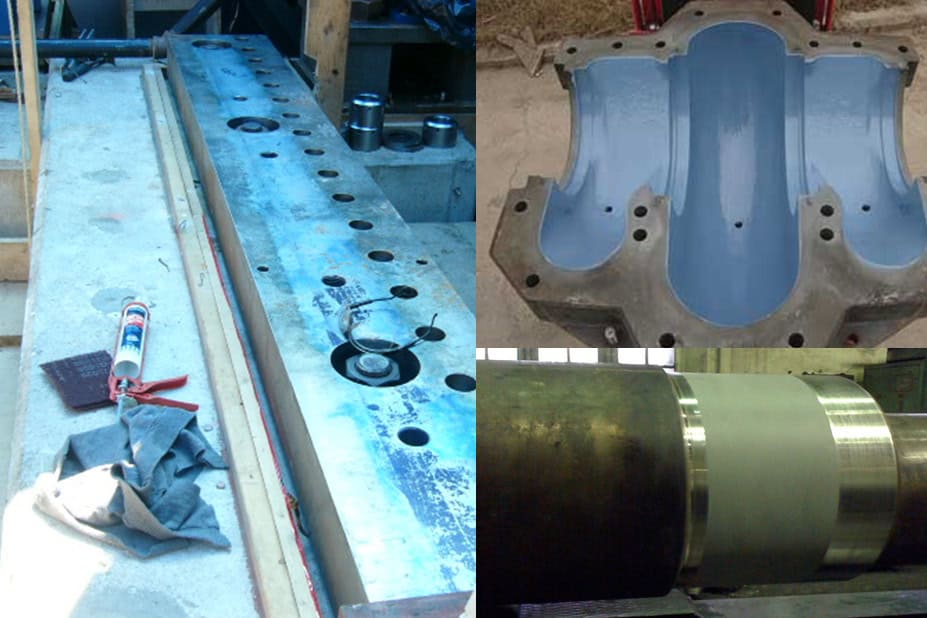
Maximum Performance Pumpable Grout (K-027)
Maximum Performance Grout is a two-component, 100 percent solid epoxy system designed for wet, underwater, high strength, and rugged, durable service. Its low component viscosity and mixed viscosity allow for efficient, problem-free meter mixing and pump dispensing into voids from 1/2″ up to 2″. Maximum Performance Grout delivers high compressive strength in extreme conditions, making it ideal for water exposure applications, including quoin and miter blocks for lock miter gates. The low viscosity and thixotropy of Maximum Performance Grout allow it to flow into narrow spaces at a rapid rate, shortening application time and assuring solid foundation support.
Common applications for Maximum Performance Grout include:
- Gyratory bottom shell placement
- Large mining cone replacement
- Pump bases
Armor Plate High-Performance Brushable Ceramic (K-096)
HP Brushable Ceramic is a two-component, high-performance ceramic-filled coating system designed for sealing, protecting, and repairing surfaces subject to high wear. HP Brushable Ceramic allows you to seal and protect equipment exposed to erosion and corrosion effectively. This solvent-free epoxy system has excellent chemical resistance.
Common uses for HP Brushable Ceramic include:
- Protect pump casings, impeller blades, gate valves, water boxes, and fan blades
- Rebuild heat exchangers, tube sheets, and other water-circulating equipment
- Use as a top coat for exceptionally smooth repaired surfaces
Armor Plate – Steel – Fast (K-081)
Armor Plate – Steel – Fast is a two-component, steel-filled epoxy designed for repairing worn shafts, sheaves, and castings or for use in tool- and die-making applications. It offers excellent corrosion resistance and resistance against a wide range of chemicals. It’s also resistant to shrinkage, expansion, and distortion. Armor Plate – Steel kits are supplied with resin and hardener pre-measured in the correct ratio, which makes for easy measuring and mixing on-site.
Common uses for Armor Plate – Steel – Fast include:
- Repairing cracks or holes in engine and pump casings, pipes, tanks, and other equipment
- Resurfacing pitted or damaged metal surfaces
- Repairing shafts and hydraulic rams
- Use as a structural adhesive for metal bonding
Products for Mine Maintenance and Beyond from Copps Industries
At Copps Industries, we offer best-in-class epoxy systems tailored for the rigorous demands of the mining industry and beyond. With standout properties and benefits, our solutions are designed to extend the life of your most critical equipment, minimize downtime, and maximize throughput.
Whether you need to deep grout large machine bases, protect equipment from erosion and corrosion, or perform quick, effective repairs, our line of epoxy products has you covered. Our solutions are engineered to help your equipment reach its full lifespan and deliver optimal performance in the harshest environments. For more information about our industrial strength solutions for heavy-duty applications, contact us and request a quote.
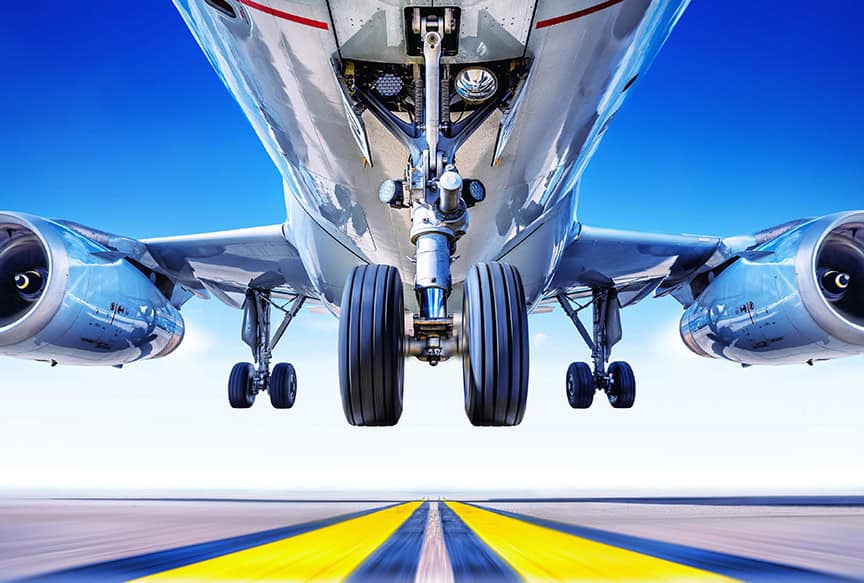
In industries where machinery and components are subject to extreme wear and tear, the importance of abrasion-resistant coatings can’t be overstated. These coatings serve as a protective shield, preventing damage and ensuring longevity. From protecting mining equipment to road vehicles to heavy manufacturing machinery, abrasion-resistant coatings are indispensable.
Copps Industries’ hard-working formulas can help you extend the lifespan of your equipment, optimize its performance, and decrease overall maintenance costs. Here, we’re demonstrating how abrasion-resistant coatings work and highlighting their benefits and wide-ranging applications.
How Abrasion-Resistant Coatings Work
Abrasion-resistant coatings safeguard surfaces from wear under harsh conditions. Typically made from durable materials like epoxies or polyurethanes, they work by forming a tough, protective layer over the surface of equipment. Abrasion-resistant coatings safeguard equipment by:
- Creating a Barrier. The coatings form a durable barrier that resists physical abrasion from dust, grit, and other particles. This prevents the underlying material from being damaged by friction and impact.
- Minimizing Friction. The coatings reduce friction between moving parts by providing a smooth surface. This protects equipment from wear and improves its efficiency and performance.
- Chemical Resistance. Many coatings also offer protection against chemicals and corrosion. This is especially important in harsh environments where equipment is exposed to aggressive substances that could degrade the material.
- Thermal Protection. Some coatings can withstand high temperatures, protecting equipment that operates in extreme heat. This thermal resistance prevents the coating from breaking down and ensures longer-lasting performance.
- Impact Resistance. The toughness of the coatings helps absorb energy from impacts, protecting equipment from dents, cracks, and other damage.
Benefits of Applying Abrasion Resistant Coating in Specific Applications
The advantages of using abrasion-resistant coatings go beyond protection. The coatings deliver various benefits that can significantly enhance performance and reduce costs. The benefits of abrasion-resistant coatings include:
- Enhanced Durability and Longevity. Abrasion-resistant coatings offer valuable protection from wear, scuffs, and scratches, improving the durability of your components and surfaces. The added durability safeguards equipment integrity and reduces the risk of premature failure, decreasing downtime and increasing longevity.
- Improved Performance and Efficiency. Abrasion-resistant coatings can reduce your downtime and maintenance costs by decreasing the need for equipment repairs. They can also minimize friction, which enhances energy efficiency, optimizes performance, and ensures smooth operation.
- Increased Safety and Reliability. Abrasion-resistant coatings protect the surface of your equipment and structures to improve their reliability and safety.
- Cost Savings and Return on Investment (ROI). Investing in abrasion-resistant coatings can deliver significant cost savings over the long run. By extending your equipment lifespan and reducing the need for replacements or repairs, these coatings save both time and money.
Applications of Abrasion-Resistant Coatings
Understanding the benefits of abrasion-resistant coatings is only part of the equation; knowing where and how to apply them is just as crucial. Abrasion-resistant coatings have wide-ranging applications across many industries, each with unique challenges and requirements. Some of the most common applications include:
Mining and Quarrying
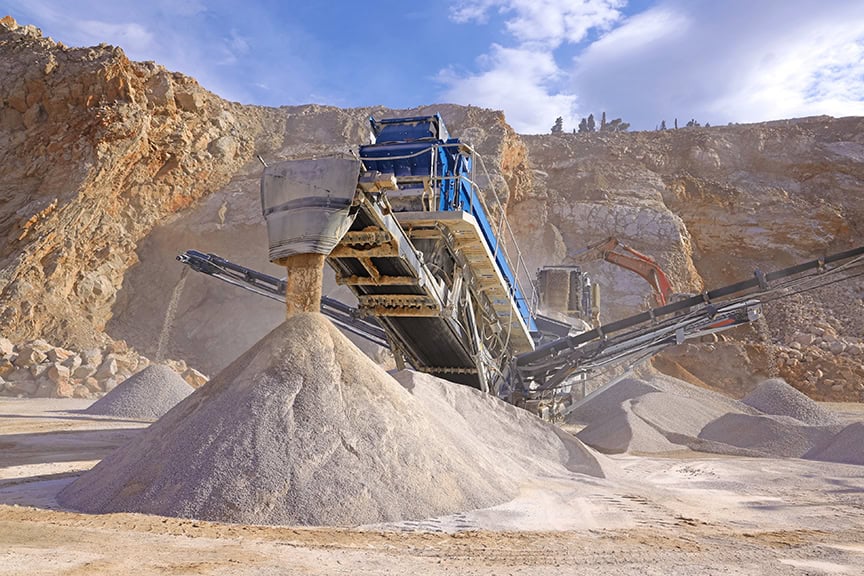
Equipment and machinery used in the mining industry are regularly subjected to abrasive environments. By applying an abrasion-resistant coating, you can protect these components from wear to increase the longevity and efficiency of the equipment while minimizing downtime. These coatings can be applied to the following types of mining and quarrying equipment:
- Crushers
- Mills
- Screens
- Mining machinery
Manufacturing and Industrial Equipment
Industrial machines and equipment are subject to friction and abrasive materials that can cause continuous wear. Abrasion-resistant coatings can be applied to polymer, concrete, and metal surfaces to protect them from abrasion caused by impact, sliding contact, and moving parts. This will help extend the lifespan of the equipment while ensuring smooth operation. The types of machinery and equipment that benefit from abrasion-resistant coatings include:
- Pump components
- Chutes and hoppers
- Agitators and mixers
- Rollers, gears, and bearings
- Conveyor belts and pulleys
Automotive and Transportation
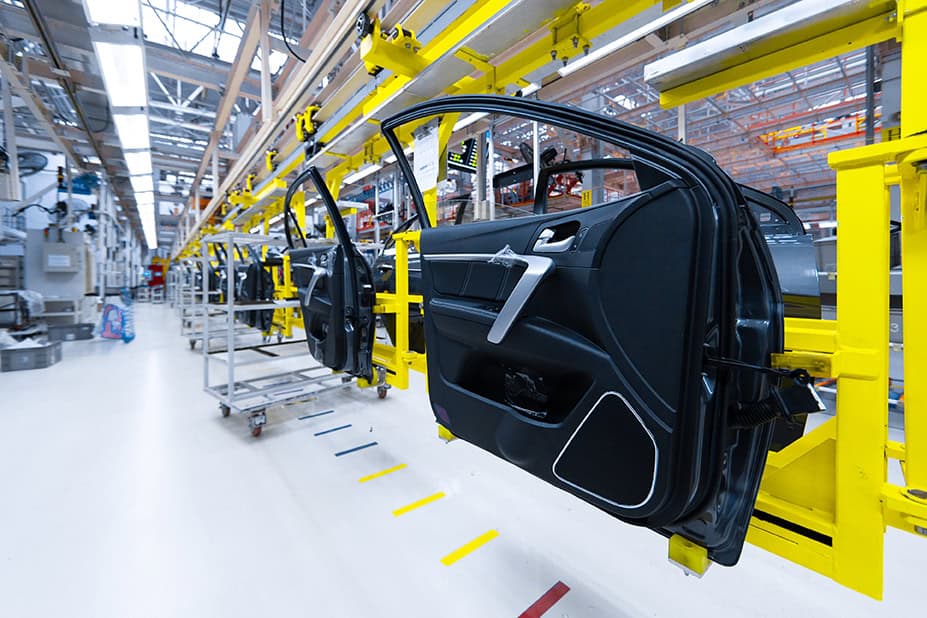
Vehicles and transportation systems are continuously exposed to sources of abrasion, including road debris, harsh environmental conditions, and even car washes. Without adequate protection, these elements can lead to paint scratches and other types of surface damage. By applying an abrasion-resistant coating, you add an extra layer of protection to preserve the appearance and value of the vehicle. Automotive applications for abrasion-resistant coatings include:
- Railway carriages
- Off-road vehicle components
- Aircraft landing gear
- Truck bed liners
- Automotive body panels
- Cargo holds
Oil and Gas
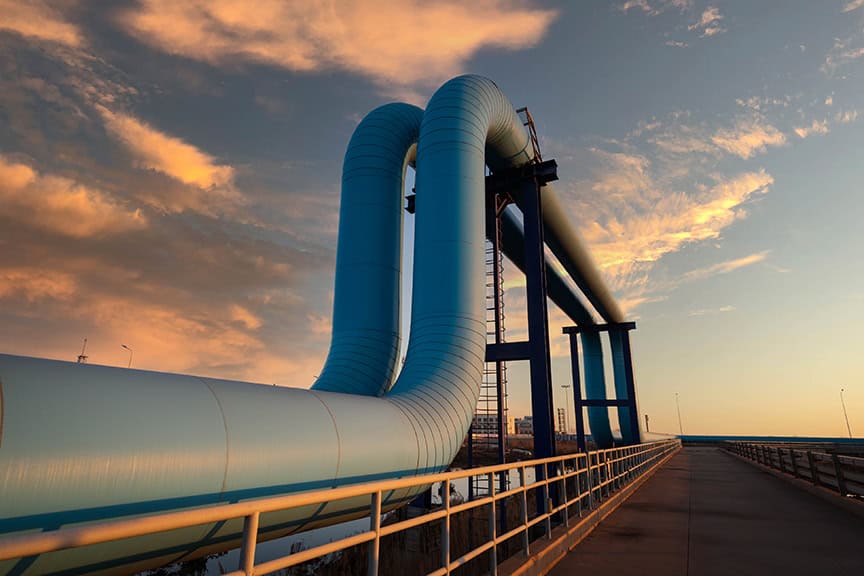
Equipment and components used in the oil and gas industry are subject to constant exposure to chemicals, abrasive materials, and harsh environmental conditions. Abrasion-resistant coatings can protect against wear and corrosion to ensure the longevity and integrity of:
- Pipes and pipelines
- Offshore platforms and rigs
- Boat decks and pontoons
- Ship hulls and marine vessels
Construction and Infrastructure
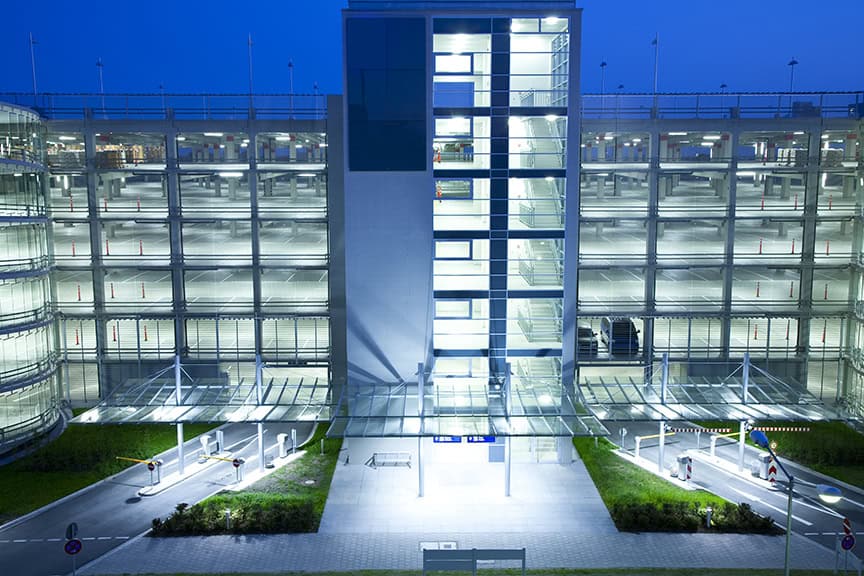
Infrastructure such as highways, parking garages, and bridges are subject to wear from environmental factors, mechanical stress, heavy vehicle and foot traffic, and chemical exposure. Abrasion-resistant coatings provide a protective barrier to prevent cracks, erosion, and surface degradation in concrete surfaces and prolong their lifespan. Common applications include:
- Concrete floors and road surfaces
- Pipeline coatings
- Tunnels and underground structures
- Bridge decks and expansion joints
Abrasion Resistant Coatings from Copps Industries
Your success depends on abrasion-resistant coatings when you operate in harsh environments and under abrasive conditions. These protective formulas can enhance the durability, safety, and cost-effectiveness of your machinery, structures, and components. From mining and manufacturing to automotive and construction, abrasion-resistant coatings are critical in extending equipment lifespan and optimizing performance.
At Copps Industries, we offer best-in-class abrasion-resistant coating solutions to meet even the most demanding conditions. Our products are designed to help your equipment reach its full lifespan and deliver the best possible performance. For more information about our abrasion-resistant coatings, contact us and request a quote.

At Copps Industries, we pride ourselves on offering customized solutions to address your challenges and meet your needs. One of the most exciting aspects of our work is developing private label solutions, a process that involves close collaboration to create epoxy formulations specifically tailored to your processes.
Here, we’re taking a peek behind the curtain with our R&D experts and giving you an in-depth look at the steps involved in developing a private label solution with Copps.
From Exploration to Excellence: 7 Steps to Your Private Label Solution
Our approach is akin to having a virtual chemist on your team. We work closely with you to ensure every aspect of the epoxy solution we develop aligns with your specific needs. Our approach brings our experts into close collaboration with you so the formulation fits seamlessly into your production processes, enhances efficiency, and minimizes costs.
Step 1: Understanding Your Needs
Our process begins with exploration. We start by discussing what you like about your existing epoxy and what improvements you need. Through a detailed consultation, our experts listen to your challenges and goals, gathering all the input they need to begin developing a custom formulation.
Step 2: Conceptualizing the Solution
Once we have a clear understanding of your needs and challenges, we move on to conceptualizing the solution. Our R&D team and chemists brainstorm and design an epoxy formulation from scratch for you.
Step 3: Formulating the Epoxy
After conceptualization, our chemists get to work in the lab to create the initial formulation. Using our expert knowledge and advanced techniques and equipment, we develop a prototype that meets your specified requirements. This stage may involve a few iterations to fine-tune the product, refining our exploration into the right solution.
Step 4: Trial and Testing
With the prototype ready, we proceed to the test phase. We thoroughly test the formulated epoxy to evaluate the product in our lab. This stage is critical as it ensures the final product will integrate seamlessly with your existing manufacturing processes, paving the way for excellence.
Step 5: Verifying and Validating
When we feel confident in the solution we’ve developed, we provide you with the formulated epoxy for testing in your production environment. This is where you get to assess the real-world application of our product and provide feedback. That feedback will help us ensure the epoxy performs as expected and meets your standards.
Step 6: Refining Based on Feedback
Based on the feedback from our lab tests and your trials, we might return to the lab to refine the formulation. Continuous exploration leads to excellence, and our goal is to deliver a solution that exceeds your expectations.
Step 7: Finalizing the Product and Partnership
Once the formulation is validated and refined, we move into full-scale production. At this stage, you can confidently integrate our customized epoxy into your manufacturing processes. But our commitment doesn’t end here; in fact, we’re just getting started. Copps Industries aims to be your partner for the long run, offering continuous support and further innovation as needed.
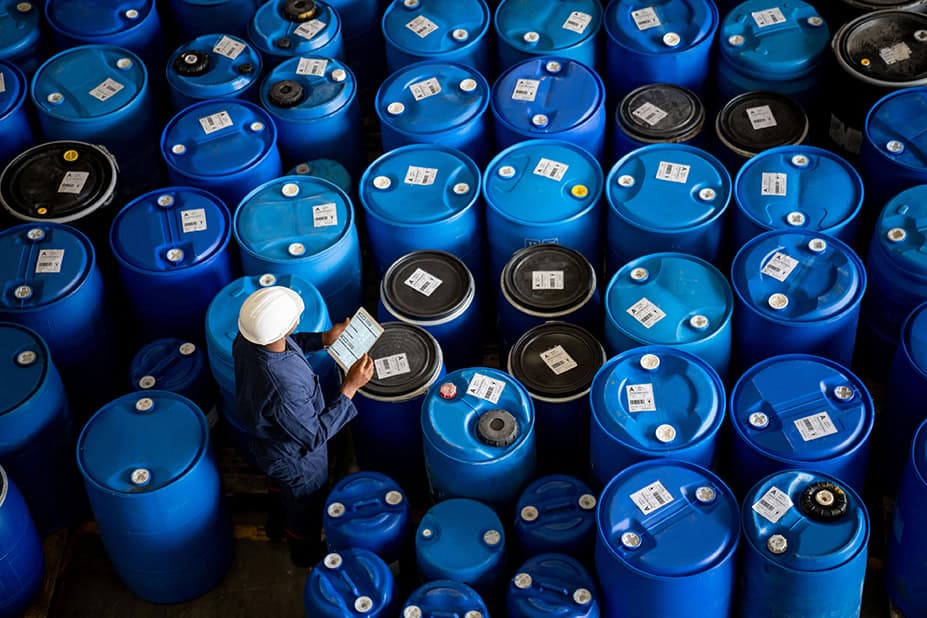
Innovation Through Partnership
Some suppliers dictate how you should use their products. At Copps Industries, we believe in innovation through partnership. We ask, “What do you need the epoxy to do?” This question, directed at engineers instead of chemists, allows us to push the boundaries of what’s possible. Once we’ve created a solution tailored to your unique needs, you won’t need to shop around—our commitment to a long-term partnership ensures you have a reliable, innovative partner by your side.
We’re also transparent about the feasibility of solutions. Sometimes, initial paper chemistry reveals that we can’t achieve a customer’s objectives. If we’re unable to meet your requirements due to health, safety, or cost concerns, we’ll be upfront about that. This honesty ensures our partnerships are built on trust and mutual respect.
Innovation with Copps Industries
At Copps Industries, we’re always eager to innovate unique private label solutions. By thinking differently and collaborating closely with our customers, we develop products that exceed expectations and set a new standard for excellence. Our approach fits various markets, allowing us to adapt formulations to any client’s specific needs.
Choosing Copps Industries for your private label epoxy solutions means partnering with a team dedicated to innovation, efficiency, and long-term success. Contact us today to learn more about how we can help you achieve your goals with tailored epoxy solutions.
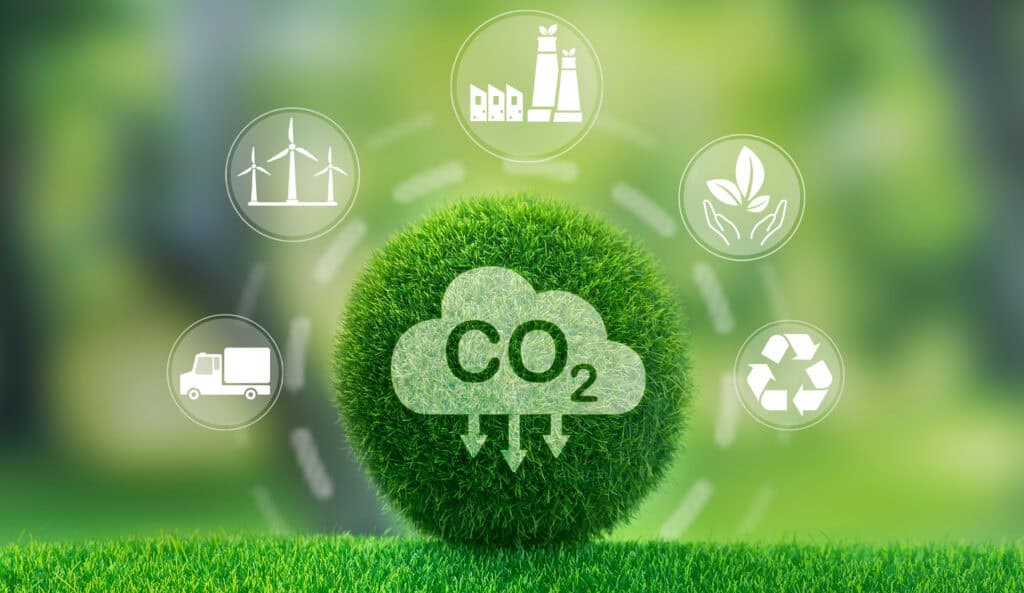
SBTi: Reinforcing Our Environmental Commitment
At Copps Industries, we take our commitment to the environment, our community, and our customers seriously. In 2023, we took an extra step to reinforce our commitment to sustainability by joining the Science Based Targets initiative (SBTi).
SBTi plays a crucial role in mobilizing the private sector to contribute to global climate goals and transition towards a low-carbon economy. The initiative offers companies a clear roadmap for sustainable growth by determining the amount and speed of reducing greenhouse gas emissions.
What Are ‘Science-Based Targets’?
Proper organization and project management initiatives can help companies zero in on social and environmental goals as part of their ESG efforts. Science-based targets, in particular, are used to denote the specific goals—and pathways to achieving those goals—that companies will use to curb greenhouse gas (GHG) emissions.
The Science-Based Targets initiative is a framework that provides a clear series of steps for companies to ensure a sufficient reduction in greenhouse gas emissions. The framework uses scientific knowledge and a deep understanding of greenhouse gases to design specific, actionable goals. A goal meets the science-based definition if it aligns with the scientific evidence in the Paris Agreement, an international treaty focused on climate change and efforts to curtail or reverse negative environmental changes.
While many organizations are motivated to reduce their climate impact and have made strides in this direction, a clear framework and widespread initiative can make the efforts more effective. To achieve real change, we all must work together on a large scale. Ambitious, scientifically-backed goals lay the groundwork for worldwide transformation.
Driving Responsible Climate Action
Companies that commit to SBTi targets are seen as leaders in sustainability and climate action.
There are many benefits of participating in SBTi:
- Transparency and accountability: Setting science-based targets allows a company to affirm its commitment to sustainability and provides a transparent framework for reporting progress against specific goals.
- Stakeholder confidence: Science-based targets assure stakeholders like customers, partners, and investors that a company is diligently managing its environmental and safety risks and working towards sustainable change.
- Regulatory preparedness: By aligning with recommended science-based targets, companies can be better prepared for future regulations and policies aimed at reducing carbon emissions.
- Operational efficiency: Setting emissions reduction targets can increase efficiency and create cost savings by helping a company improve its energy management.
Copps Industries’ Science-Based Targets: Greenhouse Gases and Environmental Commitment
Of the nearly 9,000 companies participating worldwide, around 1,200 are headquartered in North America. Most companies involved are very large; organizations like 3M, Abbott, Conagra, General Motors, and others have all declared their environmental commitment through SBTi. As a smaller company, Copps Industries’ participation is somewhat unique.
Our SBTi journey began when one of our European private-label customers brought the initiative to our attention. We listened, evaluated, and determined that participating in SBTi aligns with our mission, which reflects a commitment to the environment and commitment to our customers.
Copps Industries had a long-standing environmental commitment, continually working toward reducing our environmental impact with efforts like:
- Removing flammables from our plant
- Replacing chlorinated solvents in favor of more environmentally friendly compounds
- Removing known and suspected toxic ingredients from our chemical formulations
- Upgrading our packaging to reduce waste
Joining SBTi has allowed us to refine our goals to reduce our environmental impact. The first step in joining the initiative was signing the SBTi Commitment Letter, which allowed us to declare our commitment to SBTi publicly. After signing the letter, we had a period of time to create science-based targets that fulfilled the SBTi criteria and submit those goals for SBTi validation.
Our submission was approved using a streamlined target validation route exclusive to small and medium-sized enterprises (SMEs). Our science-based targets include a commitment to:
- Reduce scope 1 and scope 2 GHG emissions by 42% by 2030 from a 2021 base year
- Measure and reduce scope 3 emissions
Reporting and Future Goals
SBTi serves as a reporting service, and all the data that participating companies submit is publicly available on the SBTi website. The dashboard displays the organizations that have committed to set science-based targets and those with greenhouse gas (GHG) emissions reduction targets validated as science-based by the SBTi.
SBTi milestones are measured at 5, 10, and 30 years. The near-term goal of the initiative is to encourage more companies to adopt important environmental metrics. As Copps Industries’ journey evolves, regularly reporting data will allow us to ask, “Have we made an impact? How can we make changes?” We have many measures already in place and will continue to drill down on the data to identify trends and opportunities for improvement.
SBTi and the Copps Industries Mission
At Copps Industries, we support SBTi and the continued efforts toward a future with reduced or net-zero GHG emissions to slow climate change. As a leading innovator in the epoxy product space, our mission is to continually innovate our products and services to meet the needs of our customers and the environment and prioritize the safety of our employees in the workplace. We aim to continue focusing on a cleaner future and providing consistently high-quality epoxy products.
Copps Industries is your go-to partner for high-quality epoxies, but we’re also your partner for environmental action and a more sustainable supply chain. Contact us today to learn more about our initiatives or request a quote.