Category Archive: Epoxy Resins
An abrasion-resistant coating safeguards components and surfaces from wear caused by abrasive environments. Various applications depend on abrasion-resistant coatings, including mission-critical aerospace equipment, road vehicles, and heavy manufacturing machinery. Here, we will highlight the specific applications of abrasion-resistant coatings and their various advantages.
Applications of Abrasion-Resistant Coatings
Abrasion-resistant coatings are applied in various applications to prevent wear and tear. Common applications include:
Manufacturing and Industrial Equipment
Industrial machines and equipment are subject to friction and abrasive materials that can cause continuous wear. Abrasion-resistant coatings can be applied to polymer, concrete, and metal surfaces to protect them from abrasion caused by impact, sliding contact, and moving parts. This will help to extend the lifespan of equipment while ensuring smooth operation. Specific machinery and equipment that benefit from abrasion-resistant coatings include:
- Pump components
- Chutes and hoppers
- Agitators and mixers
- Rollers, gears, and bearings
- Conveyor belts and pulleys
Automotive and Transportation
Vehicles and transportation systems are continuously exposed to sources of abrasion, including road debris, car washes, and harsh environmental conditions. With adequate protection, these elements can lead to paint scratches and other types of surface damage. By applying an abrasion-resistant coating, you add an extra layer of protection to preserve the appearance and value of the vehicle. Automotive applications for abrasion-resistant coatings include:
- Railway carriages
- Off-road vehicle components
- Aircraft landing gear
- Truck bed liners
- Automotive body panels
- Cargo holds
Construction and Infrastructure
Infrastructure such as highways, parking garages, and bridges, are subject to wear from environmental factors, mechanical stress, heavy foot traffic, and chemical exposure. Abrasion-resistant coatings serve as a protective barrier to prevent cracks, erosion, and surface degradation in concrete surfaces and prolong their lifespan. Common applications include:
- Concrete floors and road surfaces
- Pipeline coatings
- Tunnels and underground structures
- Bridge decks and expansion joints
- Stadium seating and walkways
Tools and Protective Equipment
Tools, protective clothing, helmets, gloves, and other personal protective equipment (PPE) often incorporate abrasion-resistant coatings to improve protection and equipment lifespan. Specific applications include:
- Helmets and headgear
- Gloves and hand protection
- Power tool components
- Cutting blades and drill bits
- Work boots and footwear
Recreation and Sporting Goods
Abrasion-resistant coatings offer numerous advantages to recreation equipment and sporting goods that are regularly exposed to impact, weathering, and other abrasive forces. These coatings can be applied to:
- Outdoor gear
- Gloves
- Footwear
- Padding
- Helmets
Oil and Gas
Equipment and components used throughout the oil and gas industry are subject to constant exposure to chemicals, abrasive materials, and harsh environmental conditions. Abrasion-resistant coatings can protect against wear and corrosion to ensure the longevity and integrity of:
- Pipes and pipelines
- Offshore platforms and rigs
- Boat decks and pontoons
- Ship hulls and marine vessels
Mining and Quarrying
Equipment and machinery used in the mining industry are regularly subjected to abrasive environments. By applying an abrasion-resistant coating, you can protect these components from wear to increase the longevity and efficiency of the equipment while minimizing downtime. These coatings can be applied to the following types of mining and quarrying equipment:
- Crushers
- Mills
- Screens
- Mining machinery
Benefits of Applying Abrasion Resistant Coating in Specific Applications
Abrasion-resistant coatings offer several benefits, including:
- Enhanced Durability and Longevity. Abrasion-resistant coatings offer valuable shielding from wear, scuffs, and scratches, improving the durability of components and surfaces. The added durability protects equipment integrity and reduces the risk of premature failure, decreasing downtime and increasing longevity.
- Improved Performance and Efficiency. Abrasion-resistant coatings can reduce downtime and maintenance costs by decreasing the need for equipment repairs. They can also minimize friction, which enhances energy efficiency, optimizes performance, and ensures smooth operation.
- Increased Safety and Reliability. Abrasion-resistant coatings protect the surface of equipment and structures to improve reliability and safety.
- Cost Savings and Return on Investment (ROI). Investing in abrasion-resistant coatings can result in significant cost savings over the long haul. By extending equipment lifespan and reducing the need for replacements or repairs, these coatings save both time and money.
Abrasion Resistant Coatings From Copps Industries
Industries in abrasive environments depend on abrasion-resistant coatings to enhance the durability, safety, and cost-effectiveness of machinery, structures, and components. From automotive and construction to mining and manufacturing, these coatings play a critical role in extending equipment lifespan and optimizing performance.
At Copps Industries, we offer best-in-class abrasion-resistant coating solutions to meet even the most demanding challenges. Our products are designed to help your components reach their full lifespan and deliver the best possible performance. For more information about our abrasion-resistant coatings, request a quote or contact us today.
Epoxy-based coatings have been an economical choice for facility owners and designers. As a versatile coating solution, epoxies provide an aesthetic appeal, durability, chemical resistance, and surface protection from corrosion for many applications. While epoxies can be an ideal solution for surface coating, they are prone to breaking down due to exposure to light, especially ultraviolet (UV) light.
Copps Industries has been delivering epoxy resin solutions since 1979. We serve a variety of industries and applications with solutions for complex and demanding applications and harsh environments. Our custom formulations, depth of experience, and extensive portfolio allow us to deliver solutions that meet your expectations. This blog will answer the question, “Is epoxy UV resistant?” We will explore methods to protect epoxies from UV light and the benefits of using epoxies to help you determine if UV-resistant epoxy is ideal for your application.
How Does UV Light Affect Cured Epoxy?
When epoxy resin is exposed to UV light, it undergoes a process called photodegradation. The energy from the UV radiation breaks down the cured epoxy, which causes it to become weaker, discolored, and brittle.
One of the primary effects of UV exposure on cured epoxy is a reduction in its clarity and glossiness. Over time, the epoxy may start to appear cloudy, hazy, or yellowed. This is often called “ambering,” and it can be particularly noticeable on light-colored or transparent surfaces.
In addition to reducing the visual appeal of epoxy, UV exposure can also weaken its physical properties. The cured epoxy may become chalky or powdery, indicating that it has lost some of its strength. This can make it more prone to cracking, peeling, or flaking, especially if it is subjected to mechanical stress or environmental factors like moisture and temperature changes.
Prolonged exposure to UV radiation can cause irreversible damage to cured epoxy, leading to structural failure and other issues. To prevent this, it’s important to take steps to protect epoxy surfaces from UV light, such as using a UV-resistant topcoat or keeping the epoxy out of direct sunlight whenever possible.
How Can Epoxy Be Made UV Resistant?
As epoxies are not naturally UV resistant, manufacturers commonly add UV-absorbing additives to the epoxy formulation. These additives work by absorbing the UV radiation before it can penetrate and degrade the epoxy resin and hardener. By incorporating these additives, epoxy can withstand exposure to UV light for longer periods without showing significant degradation.
Another way to protect epoxy surfaces from UV damage is to use a UV-stable topcoat. This coating can be applied over the cured epoxy to act as a barrier between the epoxy and the UV radiation. The topcoat should be designed specifically for use with epoxy and should be rated for outdoor use if the surface will be exposed to direct sunlight.
The duration of UV protection for epoxy depends on the type and quality of the UV-resistant coating used, and factors such as UV exposure, climate, and coating quality can further affect the duration of protection. Regularly applying maintenance coats of UV-resistant varnish is important, with the frequency depending on the level of UV exposure and coating quality. Reapplication every one to three years, or as needed, is recommended for optimal protection.
In addition to using a UV-resistant coating or adding UV-absorbing additives to the epoxy formulation, there are other ways to protect epoxy surfaces from UV damage. For example, keeping the epoxy out of direct sunlight and using shading devices, such as awnings or umbrellas, can significantly reduce UV exposure. Regular cleaning and maintenance of the surface can also help to prolong its lifespan and protect it from UV damage.
Protecting epoxy from UV damage is essential to ensure its longevity and maintain its appearance. By choosing a UV-resistant coating or adding UV-absorbing additives to the epoxy formulation, and taking appropriate measures to minimize UV exposure, it is possible to protect epoxy surfaces from UV damage and extend their lifespan.
Advantages of Using Epoxy
While traditional epoxy is not UV resistant on its own, epoxy resins provide the following advantages:
- Durable: Epoxy resins offer good stability and durability, offering weather and chemical resistance.
- Easy to Apply: Epoxy resins can be applied quickly using a relatively simple process.
- Gap Filling: Epoxies can fill surface gaps to provide a smooth finish.
- High Strength: Epoxy resins provide a fast and strong adhesive bond to various surfaces and deliver long-term resilience and hardness.
- Versatile: Epoxy resins can be used in almost any surface coating application and can be a substitute for various other materials.
- Shrink Resistant: Epoxies are not prone to shrinkage and will not become loose once they settle properly with less than a 1% probability of shrinkage.
- Thermosetting: Once fully cured, epoxy resins will maintain their solid state and remain unaffected by high temperatures, without any melting or softening.
- Underwater: Epoxy resins are waterproof and can be used for underwater construction.
Countertop & Crafting Epoxy Resin From Copps
Epoxy resins are a preferred surface coating material for residential and commercial applications. They offer a variety of benefits, including strength, resistance to water and high temperatures, and extreme versatility. Traditional epoxies can degrade under prolonged UV light exposure and require additives or coatings to inhibit permanent photodegradation from UV light.
Copps UV-resistant countertop and crafting epoxy is easy to use and ideal for every user, from beginners to advanced artisans. Our UV-resistant craft epoxy comes in a simple, two-part system. Its self-leveling properties make it easy for users to get a perfect finish the first time. It hardens to a glass-like, crystal-clear finish to deliver lasting beauty to any countertop or crafting project. Copps has a variety of new epoxy systems with UV protection for every application. Contact us or request a quote for your UV-resistant epoxy solution.
Acrylic resin is a group of thermoplastic materials derived from acrylic acid — a monomer that is reactive with other chemicals to harden. Epoxy resin is a type of thermosetting material that can be a two-part clear liquid. Both types of resins have unique properties and applications. Copps Industries is a leading provider of epoxy resins and composite materials, offering over 500 epoxy products to customers across 27 countries.
Acrylic Resin vs. Epoxy Resin
Acrylic resin is a type of thermoplastic that can be repeatedly heated and shaped. It combines acrylic polymers with dry powders, a thin liquid, methyl methacrylate monomers, and a hardener. It’s different from epoxy resin because it can be reshaped with heat for further manipulation. Acrylic resin is strong, durable, and resistant to UV damage. This makes it ideal for a variety of applications, including outdoor use.
Epoxy resin is a thermosetting material used to create hard, durable castings, coatings, and adhesive products. It comes in a liquid form that cures quickly and adheres to different substrate materials like glass, wood, stone, concrete, and metal. The liquid epoxy is combined with a chemical hardener which cures it into hardened plastic. Once the mixture is set, it cannot be remolded or reshaped. Epoxy resins are very strong and resistant to chemicals, electrical damage, and heat. This makes them ideal for use in high-stress environments and applications requiring strength and durability.
Selecting the correct resin for your application is essential for the success of your project.
Applications
Acrylic resin is a versatile material that is used in a variety of applications, including:
- Brake lights: Acrylic resin is durable and resistant to fading, making it an ideal material for brake lights.
- Phone screens: The material is also applied to phone screens because it’s lightweight and shatter-resistant.
- Dentures: Acrylic also can mimic the appearance of natural teeth and is often used for dentures.
The strength and durability of epoxy make it ideal for industrial and commercial use, while its aesthetic properties make it popular for arts and crafts projects. Some of the most common uses for epoxy resin include:
- Adhesives: Epoxy is well-suited for adhesives because it forms a strong bond and is resistant to high temperatures and chemicals. It is commonly used to adhere metal, glass, and plastic components together.
- Industrial tools: Tools made with epoxy resin are incredibly durable and can withstand heavy use.
- Electrical components: Epoxy resin is an insulator, making it ideal for electrical applications.
- Repair and maintenance: Frequently used in repair and maintenance applications because it can effectively fill in cracks and gaps.
- Artwork: Epoxy resin can be used to create beautiful artwork. It can be cast into shapes or molded into three-dimensional designs. It can also be used as a protective coating for paintings or photographs.
Resins From Copps
Copps Industries is a leading provider of resins and composite materials. We offer a wide selection of epoxy resins suitable for applications across diverse industries. Our products are of the highest quality, and we offer competitive pricing and lead times. In addition, our team is highly knowledgeable and can assist you in choosing the right resin for your project.
Contact us today to learn more about our products and services or request a quote. You can also call us at 800.672.2622.
Epoxy resins are commonly used compounds in adhesives, paints, top coatings, sealers, and more. Most epoxy applications are combined with a specific curing process to ensure the finished product has the ideal characteristics for a given purpose. After the epoxy is applied, professionals can apply heat to speed up the curing process and create faster-forming chemical reactions. They can also keep the environment at lower temperatures to slow down the curing process and minimize molecular cross-linking in the epoxy.
Does Heat Weaken Epoxy?
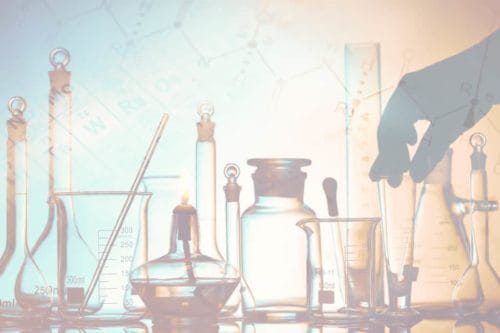
Epoxies can generally resist moderately high temperatures, with an even higher degree of resistance if the specific compound is rated as heat-resistant. However, most cured epoxy products can only be in the presence of high temperatures for a short period. Once the temperature is too high, the epoxy will grow weak, distorting and softening until it loses its shape and glassy surface.
What Temperature Is Too Hot for Epoxy?
Epoxies come in a variety of heat-resistant options, each of which can withstand different maximum temperatures before it starts to weaken. Some of the most popular types of epoxy have these temperature maximums:
- DIY or hobby epoxies: up to approximately 150°F
- High-temperature industrial epoxies: up to approximately 450°F or more
High-heat epoxies get their heat-resistant characteristics from their base molecular structure and additives such as quartz fillers. Choose the right epoxy resin for your application based on the expected temperatures it will need to handle.
How Does Cold Weather Affect Epoxy?
Cold weather has clear effects on both in-process epoxies and cured epoxies. Here are the three most important ways cold weather can affect epoxy coatings:
1. Extending Epoxy Curing Time
The lower the temperature, the longer the epoxy will take to cure. This can be advantageous for applications requiring a longer working time; however, this can extend the time (and therefore the costs) of any project.
2. Increased Humidity
Colder temperatures often increase the presence of moisture around curing epoxies. If the moisture gets into uncured epoxy and condenses into a liquid, it can blush (or cloud) the surface, creating a flat finish instead of a glassy one, and even cause defects in the surface texture.
3. Viscosity
Cold weather increases the viscosity of epoxy. This added thickness makes it more difficult to stir and can cause self-leveling epoxies to not level properly and leave imperfections.
Will Epoxy Crack when applied in Freezing Temperatures?
Temperatures lower than 50°F are considered ‘low temperatures’ for epoxies. Once the temperature dips below 50°F, there will be extended curing times. Once the temperature goes below the freezing point, or 32°F, standard epoxy won’t fully cure at all, specialty epoxies are use at these temperatures. While epoxy will not crack in freezing temperatures, it will drastically reduce its ability to cure properly.
What Can Reduce the Temperature Resistance of Epoxy?
Some additives can reduce epoxy’s resistance to temperature damage, such as solvents or improperly measured and mixed resin components. These risks can be reduced by properly following the mixing instructions.
Choose Durable Epoxies From Copps Industries, Inc.
At Copps Industries, we have specialized in producing high-quality epoxies for over 40 years. We’re committed to creating high-quality, specialty, and environmentally friendly product options for all of our clients across multiple different industries. Today, our product catalog includes more than 500 epoxy products for use in civil engineering, mining, electronics, and more, as well as 2,500 formulations in our private labeling offerings. Our company is ISO 9001:2000 certified, and we’re committed to creating products that meet our high quality standards.
Contact us today to learn more about our specialty epoxies, or request a quote for pricing details.
Epoxy resins are commonly used for adhesives, protective coatings, and other construction applications. However, some lightly colored and white epoxies can start to yellow over time, ruining the appearance of the epoxy layer. This yellowing effect can seem random, but certain environmental factors can actually make epoxy more vulnerable to yellowing. In this blog, we’ll cover some of the most common causes of epoxy yellowing and how you can prevent it.
Why Epoxy Turns Yellow
Epoxies tend to turn yellow as a result of UV radiation exposure. Although outdoor equipment is most vulnerable to this risk, indoor epoxy applications can also yellow because most windows do not sufficiently block UV radiation or lighting.
Some specialty epoxy resins can retain their original color despite prolonged sunlight exposure, but most epoxy resins will yellow over time. Here are the two most common reasons why epoxy turns yellow:
- Extended periods of high temperatures: Discoloration can happen if epoxy products sit in high temperatures for long periods of time, especially in locations without adequate climate control. Even ambient summer temperatures can accelerate yellowing. High temperatures can also damage the integrity of the epoxy resin.
- UV light exposure: Sunlight tends to make many plastics and polymers deteriorate, and epoxy resins are no exception. The epoxy molecules degrade over time as they interact with the light. This effect starts immediately, but the yellow color may not be visible until more damage accumulates.
How to Prevent Epoxy from Turning Yellow
To keep your epoxy components undamaged, you’ll need to make a preventative plan starting before the epoxy product is applied. To control heat generation, we recommend building thicker epoxy products from multiple thin layers, especially with standard epoxies. This allows each layer to properly cure at a controlled temperature. In contrast, pouring a thick mass of epoxy at once can generate enough heat to accelerate chemical reactions, resulting in cracks and discoloration. Manufacturers and hobbyists can also use specialty epoxies with UV stabilizers that are formulated to resist discoloration or handle higher heat levels.
Three key strategies for keeping epoxy from yellowing are:
- Using a sealer: Polyurethane sealants can protect the epoxy from molecular excitation in the presence of UV light and delay the discoloration process.
- Limiting UV exposure: The simplest way to prevent damage is to keep the epoxy shielded from sunlight.
- Choosing a yellow or darkly pigmented epoxy: Light-colored and white epoxy resins are the most vulnerable to yellowing. Epoxies that are already yellow or darkly colored will not show as much visible discoloration. This won’t remove the risk of cracks or other types of degradation, but it does improve the long-term appearance of epoxy.
Epoxy Resins from Copps Industries
At Copps Industries, we specialize in creating epoxy resins for commercial and industrial applications. We test every resin to ensure it meets or exceeds our quality assurance standards. Our products are built to serve diverse industries, including:
- Civil/Structural engineering
- Electrical
- Construction
- Aggregate craft epoxy
Contact Copps Industries for High-Performance Epoxy Resins
For over four decades, Copps Industries has been a leading provider of high-quality epoxy resins. Contact us today to learn about our selection of specialty and colorized epoxy products. You can also request a quote for custom pricing.
Epoxy resins are versatile materials with a high aesthetic appeal. In recent years, epoxies have gained popularity in the art world due to their limitless color options and visual appeal. Epoxies are also widely used in the bar and restaurant industries to craft unique bars and countertops. To create an epoxy resin, two liquid chemicals are mixed. When they harden, they produce a durable, low-maintenance plastic that can be used in a wide range of applications, from construction adhesive and coatings to consumer crafts.
The Different Types of Consumer Craft Epoxies
There are two primary types of epoxy resin for consumer crafts. Both types are water-clear and harden to an extremely durable finish that can withstand scratching and yellowing:
- Diamond Clear Epoxy- Tabletop: Typically used for bartops and countertops, along with artistic projects, tabletop epoxy has a medium viscosity and a 1:1 epoxy-to-hardener mix ratio. It’s used by consumers for crafts and home improvement projects, and it also has commercial and industrial applications in restaurant chains and more.
- Diamond Clear Epoxy- Casting: This low-viscosity epoxy is a favorite among woodworkers and artists. It has a 2:1 epoxy-to-hardener mix ratio and is used for large castings, river tabletops, encapsulating items, and more.
Applications of Consumer Craft Epoxies
From serving trays and coasters to tabletops and wall decor, epoxy is a versatile material limited only by the artist’s imagination. Epoxies can be made in any color, and you can pour them over a variety of other materials. Clear epoxy bar counters, for example, may feature a collection of bottle caps, pencils, or flowers underneath the hardened resin. Here are just a few of the most common craft applications for epoxies:
- Bar and Table Tops: For a high-gloss surface that exposes the underlying wood or other decorative items, epoxy offers both beauty and durable functionality. Copps offers commercial-grade epoxies that are used by bar and restaurant owners around the world.
- Casting Resin: Because these resins cure more slowly and offer a thicker pour, they are ideal for encasing or suspending objects like dried flowers, coins, and various memorabilia.
- River Tables: Thanks in part to social media how-to videos, beautiful river tables have grown in popularity. Copps consumer epoxies can be mixed with a range of pigments to create nearly any color for your river table project.
Copps Industries Private Label Program
With our private label program, Copps Industries can help you bring high-quality epoxies to market quickly. We’ve already perfected the formulation and ensured it meets all manufacturing and environmental standards and regulations, saving you time in research and development. It’s a great opportunity to extend the reach of your brand with a proven product.
Our entire line of epoxy products, featuring more than 2,500 formulations, is available for private labeling. With no start-up costs or fixed manufacturing costs, private labeling is a cost-efficient way to add an epoxy solution to your product line.
How to Choose the Optimal Private Label Manufacturing Partner
It’s important to find a private label manufacturer that values collaboration. At Copps Industries, we have years of experience in private label manufacturing, and we see ourselves as your partner in bringing your branded epoxy product to market. Working with us comes with a range of benefits, including:
- No research and development costs
- No fixed costs
- No expensive start-up costs
- No manufacturing costs
- Regulatory and environmental compliance
- Export shipping compliance
We take care of all the details, backed by our years of experience and commitment to excellence. We are ISO 9001:2015 certified and hold ourselves to the highest standards for quality, safety, and environmental responsibility. With over 2,500 formulations in our database, we have products to suit a wide variety of needs and we work to exceed your expectations. Contact us to learn more about our private label epoxy manufacturing or request a quote today.
Carbon fibers are strong, lightweight, and fatigue-resistant fibers used to build composite materials. By combining carbon fibers with epoxies, manufacturers can create incredibly hard, durable materials that outperform both individual material types. Composites are a relatively new production material compared to materials like aluminum, iron, and steel, but there are many benefits in choosing to work with carbon fiber-strengthened composites that span a range of industries.
Epoxy for Carbon Fiber
Composites are specialty materials made from a combination of fibers and resins. Epoxy resin is a thermoset polymer material that is heated and cured to chemically alter the material’s composition to create a permanently hardened substance. Most epoxy resins retain their positive attributes at temperatures as high as 175°C. Once the liquid polymers in an epoxy resin solidify, the hardened piece becomes strong, resistant to chemical and thermal damage, and can withstand physical wear or impact.
Epoxy resin is advantageous due to its properties in its liquid state. The material is a very strong adhesive with the unique ability to fuse with carbon fibers to create an even stronger microstructure that showcases the advantages of both the epoxy and the fibers.
Carbon fibers resist fatigue, have low thermal expansion, and can absorb or dampen vibrations. They are supplied in two forms that are suitable for creating composites. Carbon fiber tows are bundles of thousands of untwisted, continuous fibers which can be used directly in epoxies or converted into woven reinforcement materials like fabric or tape.
Benefits of Epoxy Resin for Carbon Fiber
Epoxy resin and carbon fiber composites are uniquely strong and offer excellent performance in commercial and industrial applications. Some of the benefits of this material include:
- Strength: Carbon fibers have very high tensile strength but are prone to damage. Epoxy resins have low tensile strength but their toughness and malleable properties protect the fibers from damage, creating an even stronger material.
- Lightweight: The composite material has an excellent strength-to-weight ratio, surpassing even aluminum and titanium. As a result, manufacturers can produce lightweight parts that can be used in more energy-efficient vehicles and assemblies.
- Flexibility: Despite its strength and durability, the composite is simultaneously very flexible. This means the material can withstand strong impact forces by absorbing the force. It also won’t develop spider cracks under impact or when the material is bent.
- No shrinkage: Epoxy resins won’t shrink after curing. This extends the lifespan of composite parts and components used in harsh environments.
- UV resistance: The composite material can withstand exposure to sunlight. It’s 100% UV resistant, so it can be used in long-term outdoor applications without the risk of wear or degradation.
- Aesthetics: Epoxy resin and carbon fiber composites are transparent, which makes them an excellent choice for visible components and consumer-facing products.
Applications of Epoxy Resins With Carbon Fiber
Epoxy resin and carbon fiber composites are very versatile, which makes them useful in a wide variety of applications and industries. At Copps Industries, we formulate epoxy resins for composite materials used across the following applications:
- Aerospace
- Aircraft and avionics
- Automotive component construction and assembly
- Boats and marine applications
- Consumer goods
- Construction
- Corrosion-resistant parts for industrial and manufacturing equipment
- Military and defense
- Oil and gas processing
- Sporting goods and recreational products
- Transportation
Choose Epoxy Resins With Carbon Fiber From Copps Industries
Since 1979, Copps Industries has been a leading provider of high-performance epoxy resins for use in civil engineering, adhesives, manufacturing, and more. Our company is ISO 9011:2015-certified as part of our commitment to excellent product quality. We produce resins for use in a wide variety of different composite materials. Contact us today to learn more about our epoxy resin formulation capabilities and services. You can also request a quote to start your order.